Underwater robot operating manipulator
A technology of underwater robots and manipulators, applied in manipulators, program-controlled manipulators, manufacturing tools, etc., can solve problems such as lack of accuracy and agility of manipulators, complex structure of hydraulic equipment, slow motion response time, etc., to improve flexibility and The effect of maneuverability, fast motion response time, and large maximum working range
- Summary
- Abstract
- Description
- Claims
- Application Information
AI Technical Summary
Problems solved by technology
Method used
Image
Examples
Embodiment 1
[0024] An underwater robot operation manipulator, which consists of: a manipulator body, a manipulator claw, a control manipulator, and an electrical cabinet; the manipulator body is composed of an electric cylinder, a rotating arm, a servo motor, an electric push rod, a large gear, and a pinion ; The manipulator claw part is composed of jaws, connecting corners, connecting rods, sliders, and push rods; the control manipulator is composed of bases, mounting seats, rotating joints, potentiometers, direction buttons and screens; The manipulator body is mechanically connected to the manipulator claw, and the manipulator body is connected to the electrical cabinet through wires, and the electrical cabinet is connected to control the manipulator through wires.
Embodiment 2
[0026] According to the underwater robot operation manipulator described in Embodiment 1, the manipulator body consists of an electric cylinder 1, an electric cylinder 2, a rotating arm 1, a rotating arm 2, a servo motor 1, a servo motor 2, an electric push rod, and a large gear , constituted by a pinion; the tail of the electric cylinder 1 is connected to the base, and a rotating shaft is installed between the tail and the head of the rotating arm 1, and the electric cylinder 1 is connected to the rotating shaft of the rotating arm 1, and the rotating arm 1. The tail is connected to the base through a rotating shaft. A rotating shaft is installed between the tail and the head of the rotating arm 2. The head of the rotating arm 1 is connected to the rotating shaft of the rotating arm 2 through a rotating shaft. The tail of the rotating arm 2 passes through The rotating shaft is connected to the push rod of the electric cylinder 2, the tail of the electric cylinder 2 is connected t
Embodiment 3
[0028] According to the underwater robot operation manipulator described in Embodiment 1, the control manipulator is composed of a rotary joint 1, a rotary joint 2, a rotary joint 3, a potentiometer 1, a potentiometer 2, a potentiometer 3, a direction button, a base, and an installation seat, wherein the base is fixed to the mounting seat, the mounting seat is fixed to the potentiometer 1, the extension shaft of the potentiometer 1 is connected to the rotary joint 1, and the rotary joint 1 rotates to drive the potentiometer 1 to rotate, and the potentiometer 1 passes through The wire is connected to the base, the potentiometer 2 is fixed to the rotary joint 1, the rotary joint 2 is connected to the extension shaft of the potentiometer 2, the rotary joint 2 rotates, and the potentiometer 2 is driven to rotate, and the potentiometer 2 is connected to the base through a wire , the potentiometer 3 is fixed to the rotary joint 2, the rotary joint 3 is connected to the extension shaft o
PUM
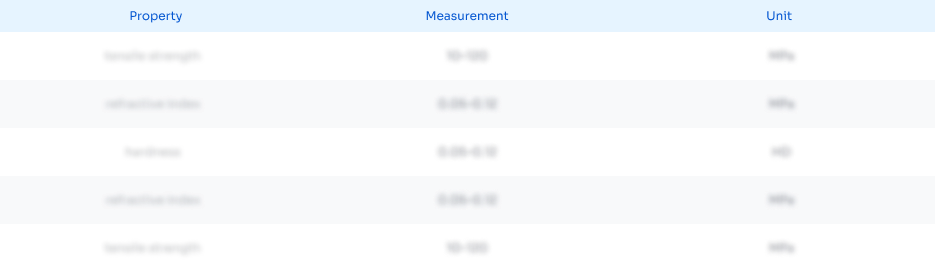
Abstract
Description
Claims
Application Information
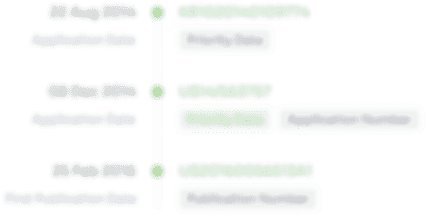
- R&D Engineer
- R&D Manager
- IP Professional
- Industry Leading Data Capabilities
- Powerful AI technology
- Patent DNA Extraction
Browse by: Latest US Patents, China's latest patents, Technical Efficacy Thesaurus, Application Domain, Technology Topic.
© 2024 PatSnap. All rights reserved.Legal|Privacy policy|Modern Slavery Act Transparency Statement|Sitemap