Sand casting die for casting of lower connecting plate
A mold and connecting plate technology, applied in the direction of manufacturing tools, casting molding equipment, casting molds, etc., can solve the problems of the number of cavity plates, reduce production efficiency, cumbersome procedures, etc., achieve low production cost, reduce production time and Effects of cost and process reduction
- Summary
- Abstract
- Description
- Claims
- Application Information
AI Technical Summary
Benefits of technology
Problems solved by technology
Method used
Image
Examples
Embodiment Construction
[0020] The present invention will be further described below in conjunction with accompanying drawing with specific embodiment:
[0021] see figure 1 , figure 2 , image 3 As shown, a sand casting mold for casting the lower connecting plate includes at least two cavity plates 1 superimposed on each other, and N cores 2, where N is an even number; the cavity plates 1 are arranged in a horizontal arrangement, The use of sand casting molds makes the production cost lower, and the cycle of the casting mold is shorter. Through the horizontal arrangement of the cavity plates 1, the connecting plates can increase the number of cavity plates 1 arranged in one molding to increase the number of moldings at one time. Reduce production time and cost; The left end face of described die cavity plate 1 is provided with concave die cavity 11, and the right end face of described die cavity plate 1 is provided with punch die cavity 12, and described punch die cavity 12 and adjacent The die cav
PUM
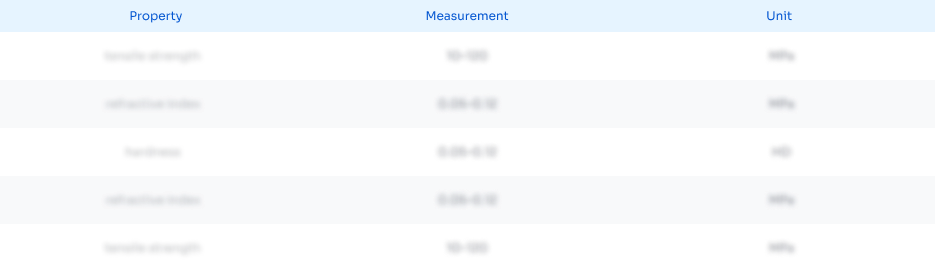
Abstract
Description
Claims
Application Information
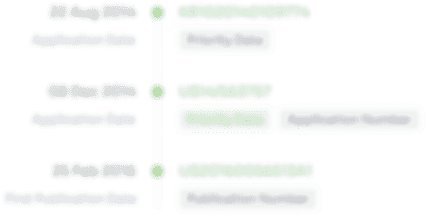
- R&D Engineer
- R&D Manager
- IP Professional
- Industry Leading Data Capabilities
- Powerful AI technology
- Patent DNA Extraction
Browse by: Latest US Patents, China's latest patents, Technical Efficacy Thesaurus, Application Domain, Technology Topic.
© 2024 PatSnap. All rights reserved.Legal|Privacy policy|Modern Slavery Act Transparency Statement|Sitemap