External thread secondary fitting fixture and clamping method
An external thread and fixture technology, which is applied to the field of secondary repairing fixtures and clamping for external threads, can solve the problems that the starting angle of the workpiece thread cannot be accurately restored, and the secondary repairing cannot be realized, and the effect of the accurate clamping method can be achieved.
- Summary
- Abstract
- Description
- Claims
- Application Information
AI Technical Summary
Problems solved by technology
Method used
Image
Examples
Embodiment Construction
[0015] 1) if figure 1 As shown, a dial fixture 1 is designed and manufactured. The inner diameter of the dial fixture 1 is larger than the outer diameter of the fixed position of the workpiece 4, and four clamping bolts 2 are uniformly distributed in the circumferential direction of the fixture, and has a U-shaped groove 3 whose width is larger than the claw 5 of the lying car.
[0016] 2) Set the dial tool 1 on the workpiece 4, and tighten the four jacking bolts 2 to fix the dial tool 1 on the workpiece 4.
[0017] 3) As attached figure 2 As shown, the workpiece 4 on which the dial tool 1 is installed is placed on the centerline of rotation of the sleeper chuck 8, and the end of the workpiece 4 that needs to be threaded faces the end of the bed. Align the top 6 at the head of the bed and the top 7 at the end of the bed to the center holes on both ends of the workpiece 4, adjust the position of the top 7 at the end of the bed to fix the workpiece 4 on the sleeping car. Rot...
PUM
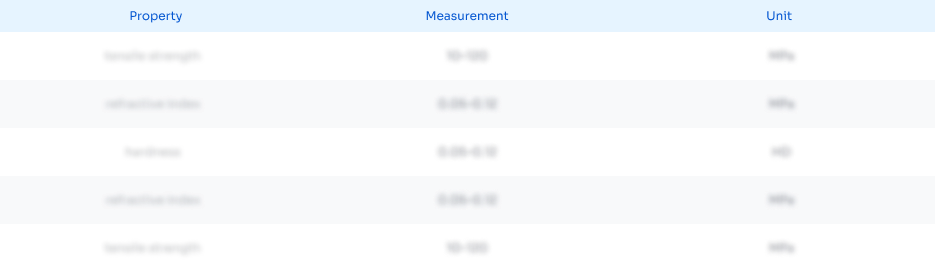
Abstract
Description
Claims
Application Information
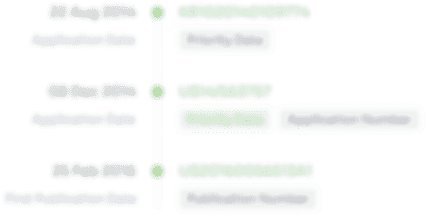
- R&D Engineer
- R&D Manager
- IP Professional
- Industry Leading Data Capabilities
- Powerful AI technology
- Patent DNA Extraction
Browse by: Latest US Patents, China's latest patents, Technical Efficacy Thesaurus, Application Domain, Technology Topic.
© 2024 PatSnap. All rights reserved.Legal|Privacy policy|Modern Slavery Act Transparency Statement|Sitemap