Optical glass, preparation method therefor and optical components thereof
An optical glass and compound technology, applied in the field of optical glass, can solve the problems of high cost, aggravated glass coloration, unfavorable high dispersion, etc., and achieve the effects of low cost, weight reduction, and low density
- Summary
- Abstract
- Description
- Claims
- Application Information
AI Technical Summary
Problems solved by technology
Method used
Image
Examples
preparation example Construction
[0077] The present invention provides a method for preparing the optical glass according to the present invention, which includes: weighing each component according to the proportion, mixing them uniformly, melting them, and then pouring or slipping them into a molding mold, or directly pressing them into shape.
[0078] Specifically, each component is weighed according to the specified ratio, mixed into batch materials, and melted in a platinum crucible at a temperature of 1230-1280 ° C. After the raw materials are melted into glass liquid, the temperature is raised to 1300-1280 ° C. 1340°C and turn on the stirrer to stir and homogenize, and the stirring time is controlled at 4-7h. After the stirring is completed, raise the temperature to 1350-1380°C and keep it warm for 5-10 hours to clarify and fully float the bubbles. Then lower the temperature to 1180-1220° C. and pour it into a molding mold, and finally process it after annealing to obtain the optical glass or optical element
Embodiment
[0088] The present invention will be described in more detail through examples below, but the present invention is not limited to these examples.
[0089] Embodiment 1-11 and ratio compare A, B, C
[0090] Table 1: Glass components and performance parameters of Examples 1-6
[0091]
[0092] Table 2: Glass components and performance parameters of Examples 7-11
[0093]
[0094] Table 3: Glass components and performance parameters of comparative examples A, B, and C
[0095]
[0096] Weigh the raw materials corresponding to the components of 1-11 examples shown in the table according to the specified proportions, mix them into batches, and melt them in a platinum crucible at a temperature of 1260°C until the raw materials are melted into glass After liquidization, the temperature was raised to 1330°C and the stirrer was turned on for stirring and homogenization, and the stirring time was controlled at 6h. After the stirring is completed, raise the temperature to 1370°C
PUM
Property | Measurement | Unit |
---|---|---|
Density | aaaaa | aaaaa |
Density | aaaaa | aaaaa |
Glass transition temperature | aaaaa | aaaaa |
Abstract
Description
Claims
Application Information
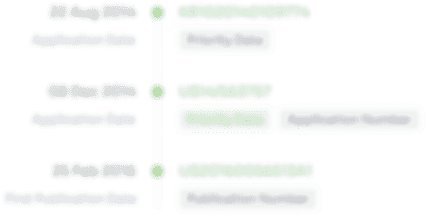
- R&D Engineer
- R&D Manager
- IP Professional
- Industry Leading Data Capabilities
- Powerful AI technology
- Patent DNA Extraction
Browse by: Latest US Patents, China's latest patents, Technical Efficacy Thesaurus, Application Domain, Technology Topic.
© 2024 PatSnap. All rights reserved.Legal|Privacy policy|Modern Slavery Act Transparency Statement|Sitemap