Method of treating manganese ore waste water
A technology for wastewater and manganese ore, applied in mining wastewater treatment, special treatment targets, multi-stage water treatment, etc., can solve the problems of polluting rivers, destroying ecological balance, occupying farmland, forests, grasslands, etc., achieving obvious effects, improving efficiency, and treating simple method effect
- Summary
- Abstract
- Description
- Claims
- Application Information
AI Technical Summary
Benefits of technology
Problems solved by technology
Method used
Examples
Embodiment 1
[0022] A method for processing manganese ore wastewater, the method may further comprise the steps:
[0023] a. Adsorption: import the manganese ore wastewater into the sedimentation tank, add carbonized materials to the manganese ore wastewater, and let it stand for 3 hours;
[0024] b. Irradiation: After the standing treatment is completed, take out the supernatant of the waste water and carry out ultraviolet irradiation treatment. The time of ultraviolet irradiation treatment is 8min, and the irradiation distance is 12cm. Then, potassium permanganate is added, and the linear speed of stirring is controlled to be 8m / Stir for 16min;
[0025] c. Secondary adsorption: continue to add carbonized materials to the supernatant after irradiation treatment, and treat for 1 hour;
[0026] d. Coagulation and discharge: add ferric sulfate to the supernatant after the secondary adsorption, stir for 16 minutes and let stand for 1 hour to separate and discharge.
[0027] Carbonized mater
Embodiment 2
[0030] A method for processing manganese ore wastewater, the method may further comprise the steps:
[0031] a. Adsorption: import the manganese ore wastewater into the sedimentation tank, add carbonized materials to the manganese ore wastewater, and let it stand for 7 hours;
[0032] b. Irradiation: After the standing treatment is completed, take out the supernatant of the waste water and carry out the ultraviolet irradiation treatment. The time of the ultraviolet irradiation treatment is 16min, and the irradiation distance is 18cm. Then, potassium permanganate is added, and the stirring line speed is controlled to be 12m / Stir for 20min;
[0033] c. Secondary adsorption: continue to add carbonized materials to the supernatant after irradiation treatment, and treat for 2 hours;
[0034] d. Coagulation and discharge: add ferric sulfate to the supernatant after secondary adsorption, stir for 20 minutes, then let stand for 1 hour to separate and discharge.
[0035] Carbonized m
Embodiment 3
[0038] A method for processing manganese ore wastewater, the method may further comprise the steps:
[0039] a. Adsorption: import the manganese ore wastewater into the sedimentation tank, add carbonized materials to the manganese ore wastewater, and let it stand for 5 hours;
[0040] b. Irradiation: After the standing treatment is completed, take out the supernatant of the waste water and carry out ultraviolet irradiation treatment. The time of ultraviolet irradiation treatment is 12min, and the irradiation distance is 15cm. Then, potassium permanganate is added, and the stirring line speed is controlled to be 15m / Stir for 18min;
[0041] c. Secondary adsorption: continue to add carbonized materials to the supernatant after irradiation treatment, and treat for 1.5h;
[0042] d. Coagulation and discharge: add ferric sulfate to the supernatant after secondary adsorption, stir for 18 minutes, then let stand for 1 hour to separate and discharge.
[0043] Carbonized material for
PUM
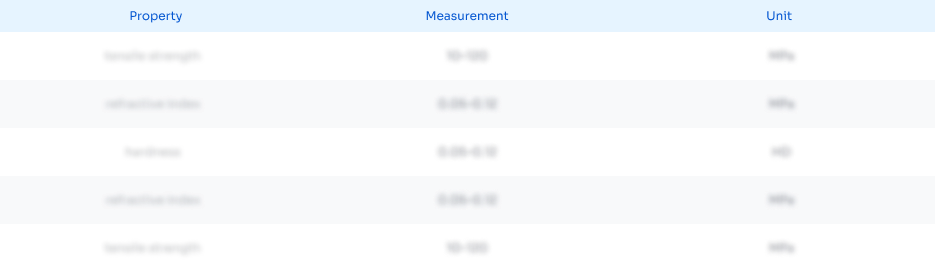
Abstract
Description
Claims
Application Information
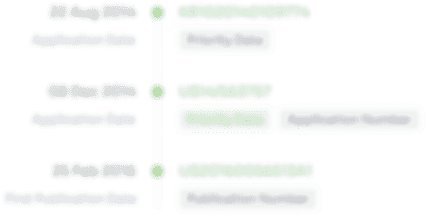
- R&D Engineer
- R&D Manager
- IP Professional
- Industry Leading Data Capabilities
- Powerful AI technology
- Patent DNA Extraction
Browse by: Latest US Patents, China's latest patents, Technical Efficacy Thesaurus, Application Domain, Technology Topic.
© 2024 PatSnap. All rights reserved.Legal|Privacy policy|Modern Slavery Act Transparency Statement|Sitemap