Miniature optical cable, method for preparing same and outer sheath material for miniature optical cable
A technology of outer sheath and optical cable, which is applied in the field of optical fiber and optical cable, can solve the problems of large limitations, unfavorable comprehensive disconnection, etc., and achieve the effect of easy control and guaranteed cable quality
- Summary
- Abstract
- Description
- Claims
- Application Information
AI Technical Summary
Benefits of technology
Problems solved by technology
Method used
Image
Examples
Embodiment 1
[0019] Such as figure 1 As shown, the present invention provides a kind of miniature optical cable, a kind of miniature optical cable, comprises cable core, and described cable core is stranded by central reinforcing steel wire 2 and several bundle tubes 3 that surround outside strengthening member, and in There are several optical fibers 1 inside the bundle tube 3; a stainless steel belt 6 is wrapped around the cable core, and a rodent-proof and flame-retardant outer sheath 4 is extruded on the outermost layer of the cable core; the stainless steel belt layer is a double-layer wrapping structure , it is not easy to be pried open by mice, which has the effect of preventing rats from biting; and coating the heat insulation film on the surface of the stainless steel belt layer, which effectively achieves the effect of heat insulation; there are several auxiliary reinforcements inserted in the rodent-proof flame-retardant sheath Wire 5.
[0020] As a further improvement, the materi
Embodiment 2
[0025] The present invention also provides a kind of preparation method of miniature optical cable, comprises the following steps:
[0026] 1) The optical fiber 1 is colored by UV curing, the fiber 1 pay-off tension is 65g±5g, the take-up tension is 75g±5g, and the production speed is 1200m / min. (Compared with conventional production, this process increases the tension of pay-off and take-up, and at the same time reduces the production speed from 2400m / min to 1200m / min.) Through this kind of process adjustment, the quality of optical fiber arrangement is guaranteed, and it is convenient for the optical fiber in the micro-bundle tube I long control.
[0027] 2) Since the outer diameter of the bundle tube 3 is only 1.6, the space inside the tube is too small. In order to reduce the fiber breakage of the optical fiber 1 in the tube, the front oil needle is changed from a squeeze tube type to a bald oil needle.
[0028] 3) The material of the bundle tube 3 is changed from PBT
Embodiment 3
[0034] The present invention also provides an outer sheath material of a miniature optical cable, comprising the following components in parts by weight: 100 parts of high-density polyethylene, 54 parts of flame retardant, 20 parts of smoke suppressant, 12 parts of EVA, 4 parts of carbon black 4 parts, 4 parts of repellent, 0.5 part of stabilizer, 0.5 part of biasing agent, 5 parts of lubricant, 5 parts of Linglong grass powder.
[0035] Wherein, the flame retardant is magnesium hydroxide, and the smoke suppressant is hydrocarbon.
PUM
Property | Measurement | Unit |
---|---|---|
Outer diameter | aaaaa | aaaaa |
Wall thickness | aaaaa | aaaaa |
Diameter | aaaaa | aaaaa |
Abstract
Description
Claims
Application Information
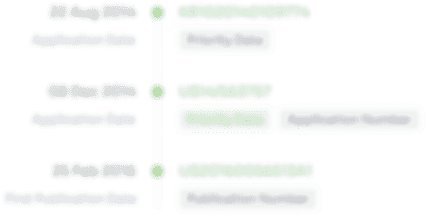
- R&D Engineer
- R&D Manager
- IP Professional
- Industry Leading Data Capabilities
- Powerful AI technology
- Patent DNA Extraction
Browse by: Latest US Patents, China's latest patents, Technical Efficacy Thesaurus, Application Domain, Technology Topic.
© 2024 PatSnap. All rights reserved.Legal|Privacy policy|Modern Slavery Act Transparency Statement|Sitemap