Method for characterizing oxidation phase of solid-phase regenerated AZ31B magnesium alloy
A technology of magnesium alloy and oxidation phase, which is applied in the field of oxidation phase characterization of solid-phase regenerated AZ31B magnesium alloy, can solve problems such as difficulty in oxidation phase characterization, and achieve the effect of increasing the size
- Summary
- Abstract
- Description
- Claims
- Application Information
AI Technical Summary
Benefits of technology
Problems solved by technology
Method used
Image
Examples
Embodiment Construction
[0028] In order to make the objects and advantages of the present invention more clear, the present invention will be further described in detail below with reference to the embodiments. It should be understood that the specific embodiments described herein are only used to explain the present invention, but not to limit the present invention.
[0029] The test material selected in this example is AZ31B wrought magnesium alloy, and the composition is shown in Table 1. The magnesium alloy as-cast billet is turned into chips of a certain size by a lathe. In this specific implementation, in order to study the morphological distribution of the oxide phase in the solid-phase regenerated magnesium alloy, the AZ31B magnesium alloy as-cast billet is turned into ultra-thin chips. , its size is: (0.01-0.02) mm × (1.48-1.52) mm × (10-200) mm, in order to increase the number of oxidized phases in the regenerated magnesium alloy and facilitate observation and analysis. , . In addition, in o
PUM
Property | Measurement | Unit |
---|---|---|
Tensile strength | aaaaa | aaaaa |
Abstract
Description
Claims
Application Information
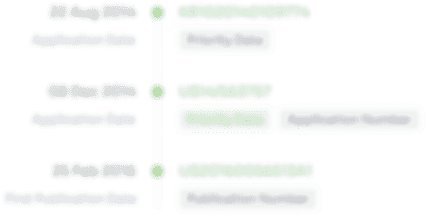
- R&D Engineer
- R&D Manager
- IP Professional
- Industry Leading Data Capabilities
- Powerful AI technology
- Patent DNA Extraction
Browse by: Latest US Patents, China's latest patents, Technical Efficacy Thesaurus, Application Domain, Technology Topic.
© 2024 PatSnap. All rights reserved.Legal|Privacy policy|Modern Slavery Act Transparency Statement|Sitemap