Blast furnace slag gasification system and method
A gasification system and blast furnace slag technology, applied in the direction of furnace, furnace components, and process efficiency improvement, can solve the problems of low utilization rate of waste heat, unutilized iron, lack of waste heat recovery technology, etc., and achieve high utilization rate of resources. Effect
- Summary
- Abstract
- Description
- Claims
- Application Information
AI Technical Summary
Problems solved by technology
Method used
Examples
Example Embodiment
[0047] Example one
[0048] (1) The coal with a carbon mass fraction of 81.51% is broken into pieces, and the blast furnace slag particles at 1380°C are granulated;
[0049] (2) Add the blast furnace slag particles and coal lumps to the blast furnace slag gasification unit at a mass ratio of 3.5:1;
[0050] (3) The moist air is introduced into the blast furnace slag gasification device through the air inlet. The coal block undergoes a gasification reaction with the moist air under the heat exchange of the blast furnace slag particles, and the gas products in the blast furnace slag gasification device exit through the coal gas. The gas port is discharged to the gas gathering device, and at the same time, the iron oxide in the blast furnace slag is reduced by the carbon in the coal;
[0051] (4) Coal ash and blast furnace slag particles produced after gasification are mixed into mixed slag and discharged through the slag outlet of the slag tray;
[0052] (5) The discharged mixed slag is cru
Example Embodiment
[0053] Example two
[0054] (1) The coal with a carbon mass fraction of 83.25% is crushed into 40mm coal lump, and 1310℃ blast furnace slag particles are granulated;
[0055] (2) Add blast furnace slag particles to coal lumps into the blast furnace slag gasification unit at a mass ratio of 5.5:1;
[0056] (3) The moist air is introduced into the blast furnace slag gasification device through the air inlet. The coal block undergoes a gasification reaction with the moist air under the heat exchange of the blast furnace slag particles, and the gas products in the blast furnace slag gasification device exit through the coal gas. The gas port is discharged to the gas gathering device, and at the same time, the iron oxide in the blast furnace slag is reduced by the carbon in the coal;
[0057] (4) Coal ash and blast furnace slag particles produced after gasification are mixed into mixed slag and discharged through the slag outlet of the slag tray;
[0058] (5) The discharged mixed slag is crush
Example Embodiment
[0059] Example three
[0060] (1) The coal with a carbon mass fraction of 84.57% is crushed into 30mm coal blocks, and the 1350℃ blast furnace slag particles are granulated;
[0061] (2) Add blast furnace slag particles and coal lumps into the blast furnace slag gasification unit at a mass ratio of 4.5:1;
[0062] (3) The moist air is introduced into the blast furnace slag gasification device through the air inlet. The coal block undergoes a gasification reaction with the moist air under the heat exchange of the blast furnace slag particles, and the gas products in the blast furnace slag gasification device exit through the coal gas. The gas port is discharged to the gas gathering device, and at the same time, the iron oxide in the blast furnace slag is reduced by the carbon in the coal;
[0063] (4) Coal ash and blast furnace slag particles produced after gasification are mixed into mixed slag and discharged through the slag outlet of the slag tray;
[0064] (5) The discharged mixed slag
PUM
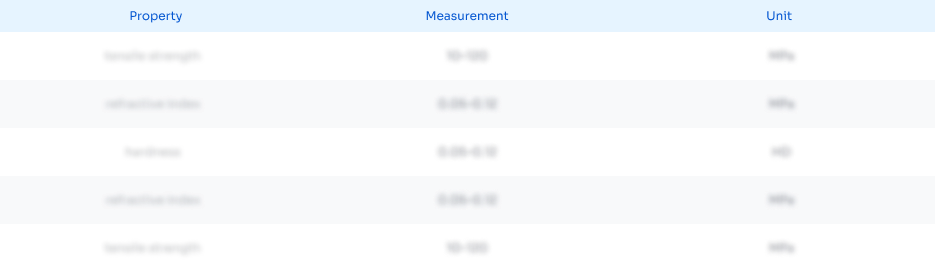
Abstract
Description
Claims
Application Information
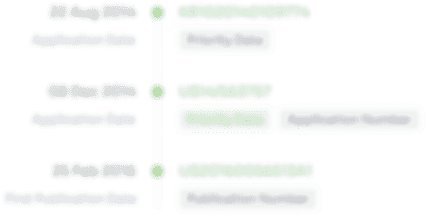
- R&D Engineer
- R&D Manager
- IP Professional
- Industry Leading Data Capabilities
- Powerful AI technology
- Patent DNA Extraction
Browse by: Latest US Patents, China's latest patents, Technical Efficacy Thesaurus, Application Domain, Technology Topic.
© 2024 PatSnap. All rights reserved.Legal|Privacy policy|Modern Slavery Act Transparency Statement|Sitemap