Forming machine for bimetallic strip
A bimetal sheet and forming machine technology, applied in metal processing equipment, feeding devices, positioning devices, etc., can solve the problems of small damage to the surface of the workpiece, thinning of the arc end of the workpiece, and short service life of the mold, etc., to achieve Improve production efficiency, avoid stretching deformation, stable and reliable operation
- Summary
- Abstract
- Description
- Claims
- Application Information
AI Technical Summary
Problems solved by technology
Method used
Image
Examples
Embodiment Construction
[0028] The present invention will be further described below in conjunction with the drawings and embodiments, but it is not a basis for limiting the present invention.
[0029] The embodiment of the present invention: a bimetal sheet forming machine, as attached Figure 1-10 As shown, the fuselage 1 is included. The top left of the fuselage 1 is provided with a feeding mechanism 2, the right side of the feeding mechanism 2 is provided with a first feeding guide 3, and the right of the first feeding guide 3 is provided with a second feeding guide 4, 2 Two feeding rails are on the same horizontal line. A cutting mechanism 5 is provided between the two feeding rails. The right side of the second feeding rail 4 is provided with a horizontal and vertical forming rail 6 which is equipped with a forming mold structure and a forming mold. The structure includes an inner mold 7, a positioning ejector 8 is provided behind the inner mold 7, a gap is left between the two, an inner mold pusher
PUM
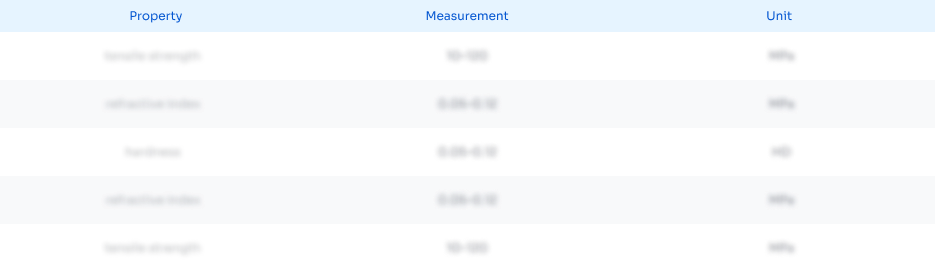
Abstract
Description
Claims
Application Information
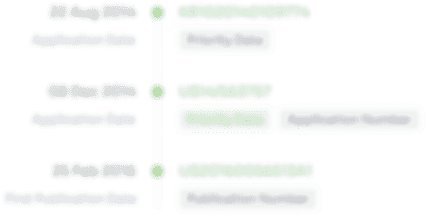
- R&D Engineer
- R&D Manager
- IP Professional
- Industry Leading Data Capabilities
- Powerful AI technology
- Patent DNA Extraction
Browse by: Latest US Patents, China's latest patents, Technical Efficacy Thesaurus, Application Domain, Technology Topic.
© 2024 PatSnap. All rights reserved.Legal|Privacy policy|Modern Slavery Act Transparency Statement|Sitemap