Six-degree-of-freedom intelligent cooperative robot
A robot and degree of freedom technology, applied in the direction of manipulators, program-controlled manipulators, joints, etc., can solve the problems of bulkiness and high quality, and achieve the effect of expanding the operating range, improving stability, and increasing length
- Summary
- Abstract
- Description
- Claims
- Application Information
AI Technical Summary
Problems solved by technology
Method used
Image
Examples
Embodiment 1
[0031] Embodiment 1: A six-degree-of-freedom intelligent collaborative robot, including a base 31, several nodes 32 and several connecting rods 33, the base 31 is fixedly connected to the nodes 32, and the nodes 32 are fixedly connected or passed through the Said connecting rod 33 is connected;
[0032] The node 32 further includes a motor 1, a brake 2, an encoder 3, a reducer 4, a transmission shaft 5 and a driver 6, and the motor 1, brake 2, encoder 3 and reducer 4 are sequentially set on the transmission shaft 5, The driver 6 is connected to the motor 1 for driving the motor 1 to rotate, and the driver 6 is connected to the encoder 3 and the brake 2 respectively;
[0033] The motor 1, the brake 2, the encoder 3, and the reducer 4 are correspondingly installed in the motor mounting shell 7, the brake mounting cover 8, the encoder mounting shell 9 and the mounting flange 10 respectively, and one side of the encoder mounting shell 9 There is a mounting groove 12 on the surface f
Embodiment 2
[0039] Embodiment 2: A six-degree-of-freedom intelligent collaborative robot, including a base 31, several nodes 32 and several connecting rods 33, the base 31 is fixedly connected to the nodes 32, and the nodes 32 are fixedly connected or passed through the Said connecting rod 33 is connected;
[0040] The node 32 further includes a motor 1, a brake 2, an encoder 3, a reducer 4, a transmission shaft 5 and a driver 6, and the motor 1, brake 2, encoder 3 and reducer 4 are sequentially set on the transmission shaft 5, The driver 6 is connected to the motor 1 for driving the motor 1 to rotate, and the driver 6 is connected to the encoder 3 and the brake 2 respectively;
[0041] The motor 1, the brake 2, the encoder 3, and the reducer 4 are correspondingly installed in the motor mounting shell 7, the brake mounting cover 8, the encoder mounting shell 9 and the mounting flange 10 respectively, and one side of the encoder mounting shell 9 There is a mounting groove 12 on the surface f
PUM
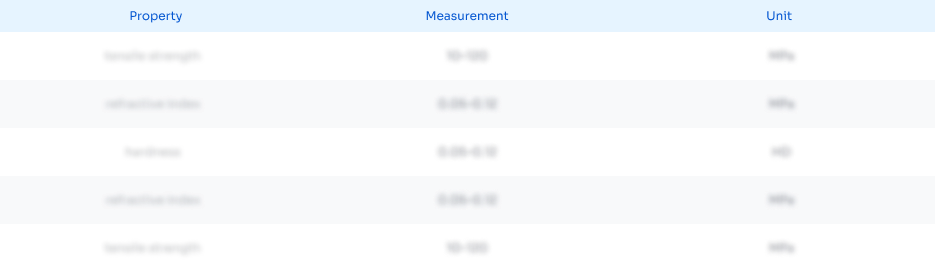
Abstract
Description
Claims
Application Information
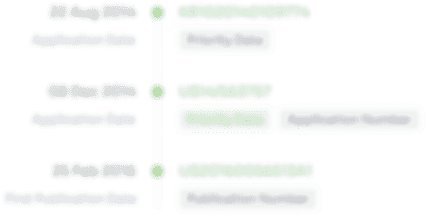
- R&D Engineer
- R&D Manager
- IP Professional
- Industry Leading Data Capabilities
- Powerful AI technology
- Patent DNA Extraction
Browse by: Latest US Patents, China's latest patents, Technical Efficacy Thesaurus, Application Domain, Technology Topic.
© 2024 PatSnap. All rights reserved.Legal|Privacy policy|Modern Slavery Act Transparency Statement|Sitemap