Aircraft servo elasticity testing analysis system and medium
A servo-elastic, aircraft technology, used in test/monitoring control systems, general control systems, electrical testing/monitoring, etc., can solve problems such as low accuracy and complex implementation, and achieve improved accuracy, reduced complexity, and improved specifications. Effects of Sex and Efficiency
- Summary
- Abstract
- Description
- Claims
- Application Information
AI Technical Summary
Problems solved by technology
Method used
Examples
Example Embodiment
[0041] Example one
[0042] The first embodiment of the present invention provides an aircraft servo elasticity test and analysis system. The structure of the system can be as follows figure 1 As shown, it includes a main control management device 11, a signal processing device 12, a frequency sweeper 13, a discrete signal input device 14, a multi-channel debugging device 15, and a variable display and analysis device 16, in which:
[0043] The main control management device 11 is configured to send respective corresponding control information to the signal processing device 12, the discrete signal input device 14, the multi-channel debugging device 15, and the variable display analysis device 16;
[0044] The signal processing device 12 is configured to send the control information sent by the main control management device to the scanner 13, and send data generated by the scanner according to the control information to the main control management device 11;
[0045] The frequency scann
Example Embodiment
[0095] Example two
[0096] The second embodiment of the present invention provides an aircraft servo resiliency test analysis method, which can be applied to a master control management device, and the step flow of the method can be as follows Figure 4 Shown, including:
[0097] Step 101: Send control information.
[0098] In this step, the main control management device can send respective corresponding control information to the signal processing device, discrete signal input device, multi-channel debugging device, and variable display analysis device.
[0099] Step 102: Receive corresponding data.
[0100] In this step, the main control management device may receive the data sent by the signal processing device, and the data sent by the discrete signal input device, the multi-channel debugging device, and the variable display and analysis device according to their corresponding control information. .
[0101] Wherein, the data sent by the signal processing device is the data generated
Example Embodiment
[0104] Example three
[0105] The third embodiment of the present invention provides an aircraft servo resiliency test and analysis method, which can be applied to signal processing equipment, and the step flow of the method can be as follows Figure 5 Shown, including:
[0106] Step 201: Receive control information.
[0107] In this step, the signal processing device can receive the control information sent by the master management device. Specifically, the control information may be an excitation parameter.
[0108] Step 202: Send control information and data.
[0109] In this step, the signal processing device can send the received control information to the scanner. And can further send the data generated according to the control information to the main control management device.
[0110] Specifically, the signal processing device may send the received excitation parameters to the scanner, and perform data fusion on the excitation data sent by the scanner and the pre-input inertial na
PUM
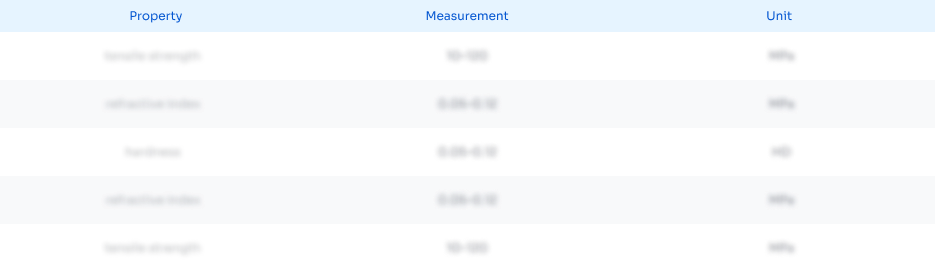
Abstract
Description
Claims
Application Information
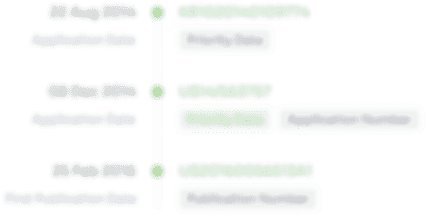
- R&D Engineer
- R&D Manager
- IP Professional
- Industry Leading Data Capabilities
- Powerful AI technology
- Patent DNA Extraction
Browse by: Latest US Patents, China's latest patents, Technical Efficacy Thesaurus, Application Domain, Technology Topic.
© 2024 PatSnap. All rights reserved.Legal|Privacy policy|Modern Slavery Act Transparency Statement|Sitemap