Method for preparing bio-based 2-phenylethanol
A phenylethanol, bio-based technology, applied in the field of preparation of bio-based 2-phenylethanol, can solve the problems of large environmental pollution, difficulty in concentration and enrichment, unsuitable for industrial production, etc., and achieve the effect of simplifying the operation process
- Summary
- Abstract
- Description
- Claims
- Application Information
AI Technical Summary
Problems solved by technology
Method used
Image
Examples
Embodiment 1
[0048] Decarboxylation operation:
[0049] In a 500mL three-neck flask, dissolve 49.56g of L-phenylalanine (0.3mol) into 200mL of cyclohexanol, add 2.88g (0.03mol) of cyclohexenone, stir evenly, then raise the temperature to 140°C, and continue heating for 12h , GC tracking until the conversion of raw materials is complete, cooling down. Underpressure distillation removes solvent cyclohexanol (solvent has no residue), obtains yellow oily liquid, and nuclear magnetic detection product structure is determined to be phenethylamine ( figure 1 ), crude product yield 98%.
[0050] Alkaline hydrolysis operation:
[0051] After re-dissolving the above liquid with 200 mL ethylene glycol diethyl ether, add 40.4 g (0.303 mol) of NaOH aqueous solution (30 wt %), heat to 220 ° C, and sample GC after 5 h to analyze the complete transformation of the intermediate. After cooling down, first add 300 mL of water to wash, and then extract with 2×200 mL of ethyl acetate. After the organic phases
Embodiment 2
[0053] Decarboxylation operation:
[0054] In a 0.5L pressure-resistant reactor, dissolve 33.04g of racemic phenylalanine (0.2mol) in 150mL of n-butanol, add 0.64g (0.007mol) of cyclohexenone, and fill the reactor with N 2 to 0.3Mpa, stir evenly, then raise the temperature to 120°C, continue heating for 24 hours, and basically stop the conversion after GC tracking the conversion rate of the raw material is 86.5%. After cooling down to stop the reaction, the reaction solution was transferred to vacuum distillation to remove the solvent n-butanol (5% solvent residue), and the crude product yield was 82%.
[0055] Alkaline hydrolysis operation:
[0056] The above-mentioned system after removal of the solvent was directly dissolved with 150 mL of glycerin (glycerol), and 27.2 mL (0.204 mol) of NaOH aqueous solution (30 wt %) was added, heated to 200 ° C, and after 10 hours, the system was sampled by GC to analyze that there was no phenylethylamine residue in the system. After cooli
Embodiment 3
[0059] Decarboxylation operation:
[0060] In a 250mL glass bottle, dissolve 16.52g of D-phenylalanine (0.1mol) into 150mL of cyclohexanol, add 0.24g (0.0025mol) of cyclohexenone, stir well, then raise the temperature to 160°C, and continue heating for 6h , GC tracked complete conversion of raw materials. After the temperature was lowered to stop the reaction, the reaction solution was transferred to vacuum distillation to remove the solvent (2% solvent remained), and the crude product yield was 95%.
[0061] Alkaline hydrolysis operation:
[0062] The above solvent-removed system was directly dissolved in 150 mL of ethylene glycol diethyl ether, 23.5 mL (0.105 mol) of KOH aqueous solution (25 wt%) was added, and heated to 250 ° C. After 3 hours, a sample was taken by GC to analyze that there was no phenylethylamine residue in the system. After cooling down, first dilute with 300mL methyl ethyl ketone and 300mL water, separate the organic phase, and remove the methyl ethyl keto
PUM
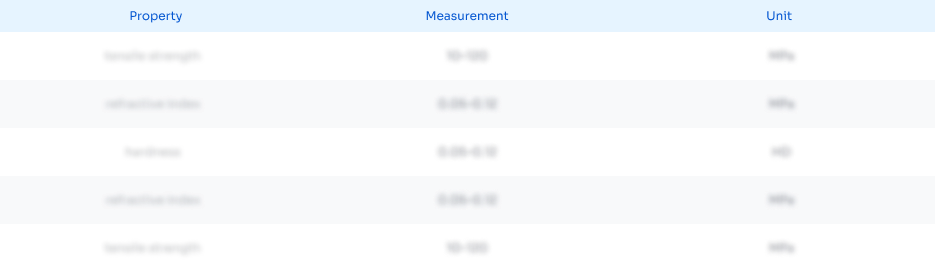
Abstract
Description
Claims
Application Information
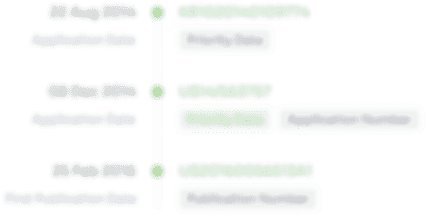
- R&D Engineer
- R&D Manager
- IP Professional
- Industry Leading Data Capabilities
- Powerful AI technology
- Patent DNA Extraction
Browse by: Latest US Patents, China's latest patents, Technical Efficacy Thesaurus, Application Domain, Technology Topic.
© 2024 PatSnap. All rights reserved.Legal|Privacy policy|Modern Slavery Act Transparency Statement|Sitemap