Preparation method of nitration catalyst and application
A nitration catalyst and catalyst technology, which can be used in catalyst activation/preparation, nitro compound preparation, physical/chemical process catalysts, etc., can solve the problem of high reaction temperature, achieve low impurity content, reduce the generation of waste acid, and be easy to separate. Effect
- Summary
- Abstract
- Description
- Claims
- Application Information
AI Technical Summary
Problems solved by technology
Method used
Examples
Example Embodiment
[0019] Example 1
[0020] Catalyst preparation: Add 5g of coconut shell activated carbon to 100mL of 20% nitric acid, stir for 8h with a magnetic stirrer at a temperature of 80℃, wash with distilled water to reach neutrality, filter and dry. After adding 100mL 30% sulfuric acid and stirring at 60°C for 6h, immersing for 0.5h, washing to neutrality, drying at 120°C, and calcining at 500°C for 2h to obtain sulfuric acid-activated carbon 1 catalyst. (20% nitric acid used for washing can be recycled)
[0021] Synthesis of 2,5-dichloronitrobenzene: Add 30g of p-dichlorobenzene into the reactor, heat to 60℃ until p-dichlorobenzene is completely melted, add 5g of the above catalyst, and slowly add dropwise to p-dichlorobenzene Nitric acid, stirring rate 600r / min, reaction temperature 60℃, constant temperature reaction for 0.5h, after reaction, the yield of 2,5-dichloronitrobenzene is 95%. Basically no waste acid is produced.
Example Embodiment
[0022] Example 2
[0023] Catalyst preparation: Add 10g of nutshell activated carbon to 200mL of 25% nitric acid, stir for 0.5h with a magnetic stirrer at a temperature of 30°C, wash with distilled water to reach neutrality, filter and dry. Add 20 g of 20% sulfuric acid solution, stir at 40°C for 6 hours, immerse for 12 hours, wash to neutrality, dry at 120°C, and calcinate at 600°C for 2 hours to obtain p-toluene sulfuric acid-activated carbon 2 catalyst.
[0024] Synthesis of 2,5-dichloronitrobenzene: Add 30g of p-dichlorobenzene into the reactor, heat to 60℃ until p-dichlorobenzene is completely melted, add 5g of the above catalyst, and slowly add dropwise to p-dichlorobenzene Nitric acid, stirring rate 1500r / min, reaction temperature 75℃, constant temperature reaction for 2h, after reaction, the yield of 2,5-dichloronitrobenzene is 91%. Basically no waste acid is produced.
Example Embodiment
[0025] Example 3
[0026] Add 5g of HY molecular sieve to 200mL of 10% hydrochloric acid, stir for 4h with a magnetic stirrer at a temperature of 30℃, wash with distilled water to reach neutrality, filter and dry. Add 20g of 10% hydrochloric acid solution, stir at 10°C for 6h, immerse for 24h, wash to neutrality, dry at 120°C, and calcinate at 400°C for 2h to obtain salt-HY catalyst.
[0027] Synthesis of 2,5-dichloronitrobenzene: Add 30g of p-dichlorobenzene into the reactor, heat to 60℃ until p-dichlorobenzene is completely melted, add 5g of the above catalyst, and slowly add dropwise to p-dichlorobenzene Nitric acid, stirring rate 1200r / min, reaction temperature 80℃, constant temperature reaction for 1h, after reaction, the yield of 2,5-dichloronitrobenzene is 80.5%. Basically no waste acid is produced.
PUM
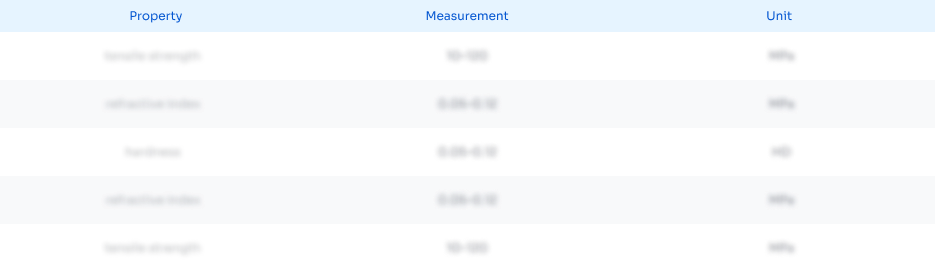
Abstract
Description
Claims
Application Information
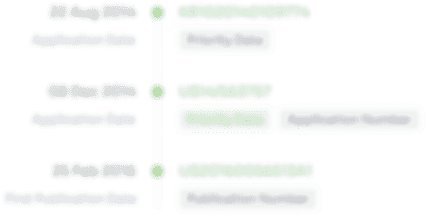
- R&D Engineer
- R&D Manager
- IP Professional
- Industry Leading Data Capabilities
- Powerful AI technology
- Patent DNA Extraction
Browse by: Latest US Patents, China's latest patents, Technical Efficacy Thesaurus, Application Domain, Technology Topic.
© 2024 PatSnap. All rights reserved.Legal|Privacy policy|Modern Slavery Act Transparency Statement|Sitemap