Repairing method for eliminating clutters generated during ultrasonic flaw detection of high-temperature alloy
A technology of superalloy and repair method, which is applied to the analysis of solids using sonic/ultrasonic/infrasonic waves, preparation and sampling of samples for testing, etc. Morphological differences, eliminating uneven flaw detection, improving quality and stability
- Summary
- Abstract
- Description
- Claims
- Application Information
AI Technical Summary
Problems solved by technology
Method used
Image
Examples
Embodiment
[0028] Embodiment: A kind of repairing method that eliminates superalloy produces clutter during ultrasonic flaw detection, such as figure 1 shown, including the following steps:
[0029] S1. Heating: Heat the coarse-grained forging 3 to the solid solution temperature. The range of the solid solution temperature is based on the solid solution temperature of the alloy. 90min~120min. The forging 3 is transformed into a solid solution again, and then various alloy phases in the forging 3 are re-dissolved.
[0030] Afterwards, the forging 3 is kept warm for 90 minutes to 120 minutes, which is consistent with the solid solution heat preservation time. The heat preservation is to ensure that the alloy structure of the forging 3 is fully transformed into a solid solution state.
[0031] S2. Mold 2 preparation: The staff preheats the mold 2. The preheating temperature range is 120-150°C. After that, the mold 2 is kept warm for a period of time, and the holding time is ≥8-12h, so as to
PUM
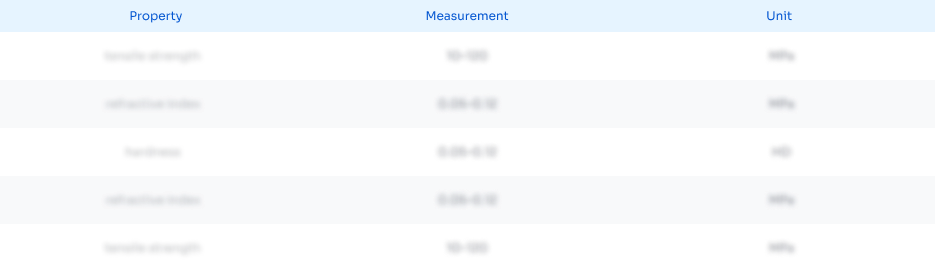
Abstract
Description
Claims
Application Information
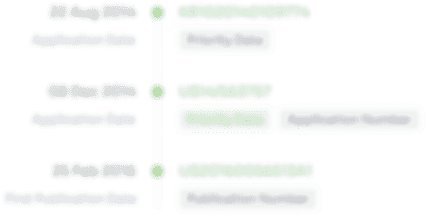
- R&D Engineer
- R&D Manager
- IP Professional
- Industry Leading Data Capabilities
- Powerful AI technology
- Patent DNA Extraction
Browse by: Latest US Patents, China's latest patents, Technical Efficacy Thesaurus, Application Domain, Technology Topic.
© 2024 PatSnap. All rights reserved.Legal|Privacy policy|Modern Slavery Act Transparency Statement|Sitemap