Manufacturing method of anode target, anode target, X-ray source and X-ray imaging system
A production method and anode target technology, applied in the field of X-rays, can solve the problems of long production cycle, high technical difficulty, low processing precision, etc., and achieve the effect of reducing production difficulty and solving production difficulties
- Summary
- Abstract
- Description
- Claims
- Application Information
AI Technical Summary
Problems solved by technology
Method used
Examples
Example Embodiment
[0037] Example 1
[0038] like figure 1 As shown, the first embodiment of the present invention provides a method for manufacturing an anode target, and the method for manufacturing an anode target includes:
[0039] S110, forming periodically arranged first trenches on the substrate.
[0040] In this embodiment, the material of the substrate can be a material with high hardness, such as diamond, and preferably, the processing method for forming a plurality of periodically arranged first grooves on the substrate includes using plasma etching technology, precision machining technology or one of femtosecond laser processing technology.
[0041] Specifically, the periodically arranged first grooves include: grooves arranged in a meander shape, a zigzag shape or an S-shape; or a plurality of grooves arranged in parallel and spaced apart. Wherein, the grooves arranged in a meander, zigzag or S-shape include: a plurality of first sub-grooves arranged in parallel along a first direct
Example Embodiment
[0056] Embodiment 2
[0057] like Figure 8 As shown, the second embodiment of the present invention provides an anode target, and the anode target is manufactured by using the method for manufacturing the anode target provided in the first embodiment of the present invention.
[0058] In one embodiment, the anode target includes a substrate 801 , a first trench 802 , and a metal tungsten wire 803 .
[0059] Specifically, the material of the substrate 801 can be made of a material with high hardness, such as diamond. Preferably, the processing method for forming a plurality of periodically arranged first grooves 802 on the substrate 801 includes using plasma etching technology, precision machinery One of cutting technology or femtosecond laser processing technology.
[0060] Specifically, the periodically arranged first grooves 802 include: grooves arranged in a meander shape, a zigzag shape or an S shape, such as image 3 and Figure 4 shown; or multiple grooves spaced in pa
Example Embodiment
[0064] Embodiment 3
[0065] like Figure 9 As shown, the third embodiment of the present invention provides an X-ray source. The X-ray source includes a cathode 905 , a high-voltage power supply 906 , a tube case 907 , an anode 908 and a transmission window 910 .
[0066] In this embodiment, the anode 908 includes an anode substrate 901, an anode target 902 and an anode cap 909. The anode target 902 adopts the anode target provided in the second embodiment of the present invention, and the cathode 905 includes a cathode cover 911, a cathode filament lead 903 and a cathode filament 912. , the high voltage power supply 906 is respectively electrically connected to the cathode 905 and the anode target 902 , the cathode 905 and the anode 908 are sealed in the high vacuum tube 907 , and the transmission window 910 is arranged outside the anode 908 .
[0067] When using the X-ray source, turn on the high-voltage power supply 906, make the cathode filament 912 of the cathode 905 emit
PUM
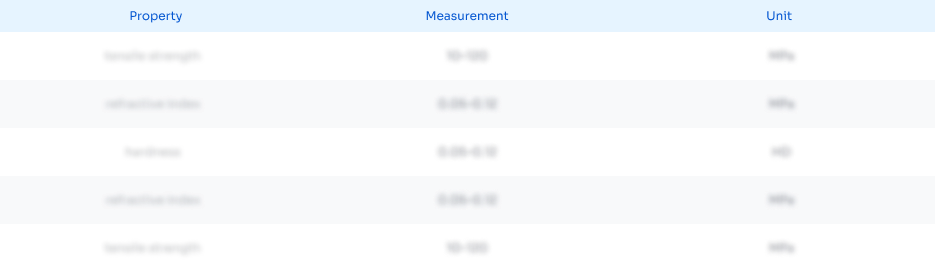
Abstract
Description
Claims
Application Information
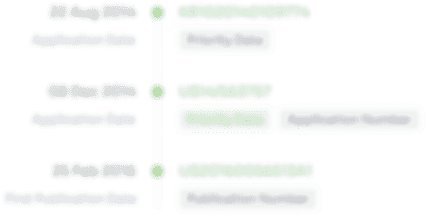
- R&D Engineer
- R&D Manager
- IP Professional
- Industry Leading Data Capabilities
- Powerful AI technology
- Patent DNA Extraction
Browse by: Latest US Patents, China's latest patents, Technical Efficacy Thesaurus, Application Domain, Technology Topic.
© 2024 PatSnap. All rights reserved.Legal|Privacy policy|Modern Slavery Act Transparency Statement|Sitemap