Double-station sheet stamping die
A thin-plate stamping and double-station technology, applied in the field of stamping, can solve problems such as low stamping efficiency and achieve the effect of improving stamping efficiency
- Summary
- Abstract
- Description
- Claims
- Application Information
AI Technical Summary
Benefits of technology
Problems solved by technology
Method used
Image
Examples
Embodiment Construction
[0015] The present invention will be further described in detail below in conjunction with the accompanying drawings and embodiments.
[0016] like figure 1 and 2 As shown, the double-station thin plate stamping die in the implementation of the present invention includes a stamping base 1, an upper fixed mold 21, a guide post 24, an upper template 23, an upper movable mold 22, a side stamping table 12, a side fixed mold 31, and a side movable Die 32, first spring 25, second spring 523, first air pump 41, second air pump 42, electromagnet 33, stamping motor 7, rotating disk 8, first stamping column 51, second stamping column 52, first sphere 511 , the second sphere 521 , the transmission rack 524 and the stamping rack 35 .
[0017] Wherein, the upper fixed mold 21 is arranged on the upper side of the stamping base 1, the guide post 24 is erected on the upper side of the stamping base 1, the upper template 23 is slidably arranged on the guide post 24, and the upper movable mold 2
PUM
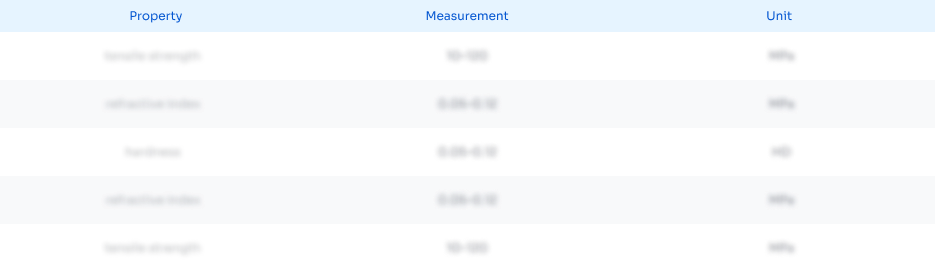
Abstract
Description
Claims
Application Information
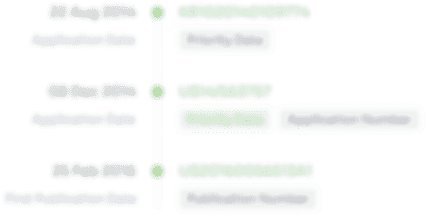
- R&D Engineer
- R&D Manager
- IP Professional
- Industry Leading Data Capabilities
- Powerful AI technology
- Patent DNA Extraction
Browse by: Latest US Patents, China's latest patents, Technical Efficacy Thesaurus, Application Domain, Technology Topic.
© 2024 PatSnap. All rights reserved.Legal|Privacy policy|Modern Slavery Act Transparency Statement|Sitemap