Waste and old film-coated paper recycling preparation process
A preparation process and technology of coated paper, which is applied in the field of waste paper recycling, can solve the problems affecting the cleanliness of paper and excessive impurities, and achieve the effects of improving water filtration rate, reducing accumulation, and reducing pollution
- Summary
- Abstract
- Description
- Claims
- Application Information
AI Technical Summary
Problems solved by technology
Method used
Image
Examples
Example Embodiment
[0029] Example 1:
[0030] A process for recycling and preparing waste coated paper includes the following steps:
[0031] Step 1: After removing the impurity of the coated paper, put it into the oven to remove the film, so that the coating film on the coated paper will melt and condense;
[0032] Step 2: Put the film-removed coated paper into boiling water for cooking, the boiling water is weakly alkaline boiling water, the added reagent is calcium hydroxide aqueous solution, the concentration of calcium hydroxide is 1.5mol / L, and it is removed after cooking for 10 minutes;
[0033] Step 3: Drain the removed coated paper with water and add it to a pulverizer for pulverization. The particles of the pulverized coated paper are 100 meshes, and the time for ultrasonic vibration to disperse the pulp particles is 12 minutes;
[0034] Step 4: After sterilizing, the pulp mixture is allowed to stand for 1 hour, and then filtered with a fine screen to obtain the final pulp, which is poured into a
Example Embodiment
[0035] Example 2:
[0036] A process for recycling and preparing waste coated paper includes the following steps:
[0037] Step 1: After removing the impurity of the coated paper, put it into the oven to remove the film, so that the coating film on the coated paper will melt and condense;
[0038] Step 2: Put the film-removed coated paper into boiling water for cooking, the boiling water is weakly alkaline boiling water, the added reagent is calcium hydroxide aqueous solution, the concentration of calcium hydroxide is 2mol / L, and it is removed after cooking for 11 minutes;
[0039] Step 3: Drain the removed coated paper with water and add it to a pulverizer for pulverization. The particles of the pulverized coated paper are 140 meshes, and the time for ultrasonic vibration to disperse the pulp particles is 15 minutes;
[0040] Step 4: After sterilizing, the pulp mixture is allowed to stand for 1.2 hours, and then filtered with a fine screen to obtain the final pulp, which is poured into
Example Embodiment
[0041] Example 3:
[0042] A process for recycling and preparing waste coated paper includes the following steps:
[0043] Step 1: After removing the impurity of the coated paper, put it into the oven to remove the film, so that the coating film on the coated paper will melt and condense;
[0044] Step 2: Put the film-removed coated paper into boiling water for cooking, the boiling water is weakly alkaline boiling water, the added reagent is calcium hydroxide aqueous solution, the concentration of calcium hydroxide is 2.4mol / L, and it is removed after cooking for 12 minutes;
[0045] Step 3: Drain the removed coated paper with water and add it to a pulverizer for pulverization. The particles of the pulverized coated paper are 180 meshes, and the time for ultrasonic vibration to disperse the pulp particles is 20 minutes;
[0046] Step 4: After disinfection, the pulp mixture is allowed to stand for 1.4 hours, and then filtered with a fine screen to obtain the final pulp, which is poured in
PUM
Property | Measurement | Unit |
---|---|---|
Concentration | aaaaa | aaaaa |
Concentration | aaaaa | aaaaa |
Concentration | aaaaa | aaaaa |
Abstract
Description
Claims
Application Information
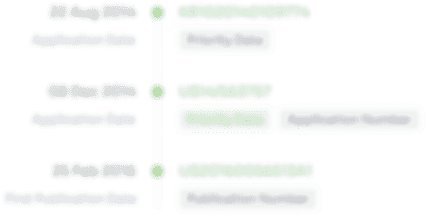
- R&D Engineer
- R&D Manager
- IP Professional
- Industry Leading Data Capabilities
- Powerful AI technology
- Patent DNA Extraction
Browse by: Latest US Patents, China's latest patents, Technical Efficacy Thesaurus, Application Domain, Technology Topic.
© 2024 PatSnap. All rights reserved.Legal|Privacy policy|Modern Slavery Act Transparency Statement|Sitemap