Treatment method for gradient utilization of steel slag
A disposal method, steel slag technology, applied in the direction of recycling technology, process efficiency improvement, solid separation, etc., can solve the problems of short service life of wear-resistant devices, unable to achieve more crushing and less grinding, unsatisfactory crushing effect, low metal recovery rate, etc. , to achieve the effect of reducing engineering construction costs, realizing economic value, and ensuring the production environment
- Summary
- Abstract
- Description
- Claims
- Application Information
AI Technical Summary
Problems solved by technology
Method used
Image
Examples
Embodiment 1
[0035] The disposal method of a kind of steel slag cascade utilization that the present invention proposes, comprises the following steps:
[0036] S1 pre-crushing: Pre-crushing the steel slag with a jaw crusher, with a particle size of 5mm, and then secondary crushing of the pre-crushed steel slag, with a particle size of 1mm;
[0037] S11: Add potassium sodium tartrate to the steel slag after secondary crushing, and continue to stir and mix it for 5 minutes, and the mass ratio of steel slag to potassium sodium tartrate is 100:0.01;
[0038] S2 Magnetic Separation: Re-screen secondary crushed steel slag, steel slag with a particle size of less than 5mm is sent to the strong magnetic machine equipment, and iron fine particles with Mfe>60% are selected and stacked on the ground, and steel slag with a particle size larger than 5mm is returned to the raw material bin to continue Perform secondary crushing to form a closed loop;
[0039] S3 wet grinding: the remaining steel slag in
Embodiment 2
[0046] The disposal method of a kind of steel slag cascade utilization that the present invention proposes, comprises the following steps:
[0047] S1 pre-crushing: Pre-crushing the steel slag with a jaw crusher, with a particle size of 10mm, and then secondary crushing of the pre-crushed steel slag, with a particle size of 3mm;
[0048] S11: Add potassium sodium tartrate to the steel slag after secondary crushing, and continue to stir and mix it for 7 minutes, and the mass ratio of steel slag to potassium sodium tartrate is 100:0.02;
[0049] S2 Magnetic Separation: Re-screen secondary crushed steel slag, steel slag with a particle size of less than 5mm is sent to the strong magnetic machine equipment, and iron fine particles with Mfe>60% are selected and stacked on the ground, and steel slag with a particle size larger than 5mm is returned to the raw material bin to continue Perform secondary crushing to form a closed loop;
[0050] S3 wet grinding: the remaining steel slag in
Embodiment 3
[0057] The disposal method of a kind of steel slag cascade utilization that the present invention proposes, comprises the following steps:
[0058] S1 pre-crushing: Pre-crushing the steel slag with a jaw crusher, with a particle size of 30mm, and then secondary crushing of the pre-crushed steel slag, with a particle size of 4mm;
[0059] S11: Add potassium sodium tartrate to the steel slag after secondary crushing, and continue to stir and mix it for 9 minutes, and the mass ratio of steel slag to potassium sodium tartrate is 100:0.02;
[0060] S2 Magnetic Separation: Re-screen secondary crushed steel slag, steel slag with a particle size of less than 5mm is sent to the strong magnetic machine equipment, and iron fine particles with Mfe>60% are selected and stacked on the ground, and steel slag with a particle size larger than 5mm is returned to the raw material bin to continue Perform secondary crushing to form a closed loop;
[0061] S3 wet grinding: the remaining steel slag in
PUM
Property | Measurement | Unit |
---|---|---|
Particle size | aaaaa | aaaaa |
Abstract
Description
Claims
Application Information
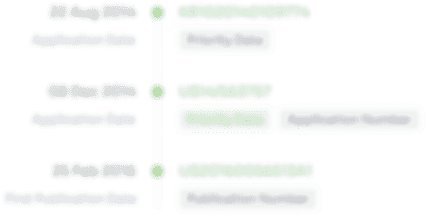
- R&D Engineer
- R&D Manager
- IP Professional
- Industry Leading Data Capabilities
- Powerful AI technology
- Patent DNA Extraction
Browse by: Latest US Patents, China's latest patents, Technical Efficacy Thesaurus, Application Domain, Technology Topic.
© 2024 PatSnap. All rights reserved.Legal|Privacy policy|Modern Slavery Act Transparency Statement|Sitemap