Double-pump separate-cavity adjusting control load simulation system
A technology of regulation control and load simulation, applied in the field of aviation simulation, can solve the problems of low precision, low energy efficiency of the simulation loading system, and poor anti-interference performance, and achieve the effect of high energy efficiency and high precision load simulation tasks
- Summary
- Abstract
- Description
- Claims
- Application Information
AI Technical Summary
Problems solved by technology
Method used
Image
Examples
Embodiment Construction
[0019] The present invention will be further described below in conjunction with the accompanying drawings.
[0020] like figure 1 As shown, the embodiment of the present invention is a double-pump sub-chamber regulation control load simulation system, including a simulator loading system and a steering gear system, including a simulator loading system and a steering gear system connected to each other, and the simulator loading system includes a pump control flow rate Servo subsystem, pump control pressure servo subsystem, first bidirectional quantitative pump 14 and second bidirectional quantitative pump 10, the hardware composition of the pump control flow servo subsystem includes: loading actuator 1, speed sensor 2, steering gear speed differential Unit, speed servo controller 8 , speed instruction calculation unit 11 and loading controller 13 , the hardware composition of the pump control pressure servo subsystem includes force sensor 3 . The steering gear system includes a
PUM
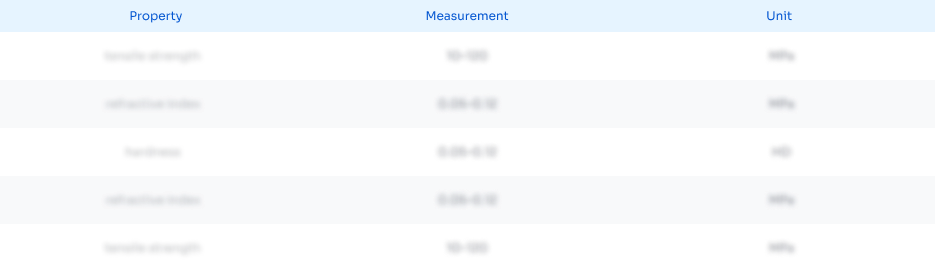
Abstract
Description
Claims
Application Information
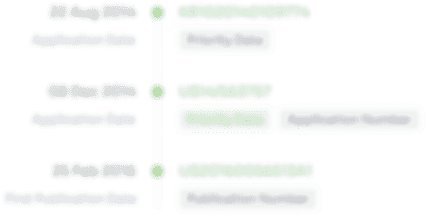
- R&D Engineer
- R&D Manager
- IP Professional
- Industry Leading Data Capabilities
- Powerful AI technology
- Patent DNA Extraction
Browse by: Latest US Patents, China's latest patents, Technical Efficacy Thesaurus, Application Domain, Technology Topic.
© 2024 PatSnap. All rights reserved.Legal|Privacy policy|Modern Slavery Act Transparency Statement|Sitemap