Smelting method of carbon-free sponge iron
A smelting method and carbon-free sponge technology, applied in chemical instruments and methods, inorganic chemistry, furnaces, etc., can solve the problems of high production cost, low production capacity, and complicated preparation methods of high-purity iron, and achieve the elimination of reducing atmosphere and the limit of dephosphorization high effect
- Summary
- Abstract
- Description
- Claims
- Application Information
AI Technical Summary
Benefits of technology
Problems solved by technology
Method used
Image
Examples
Embodiment 1
[0086] Mix 10kg of sponge iron and quicklime (CaO) at a mass ratio of 1:0.042 to 0.069 and put it into a vacuum induction furnace with a capacity of 30kg of molten iron for smelting. The binary alkalinity of the mixture of sponge iron and quicklime (CaO) is controlled at The range of 2.5 to 4.0, the composition of sponge iron is shown in Table 1.
[0087] Table 1 Sponge iron composition
[0088] sponge iron ingredients TF MFe FeO CaO SiO 2
MgO Al 2 o 3
P S content(%) 94.133 87.614 9.313 0.314 1.805 0.793 1.174 0.236 0.003
[0089] After the separation of slag and iron is complete, the molten iron passes through the taphole at the lower part of the induction furnace to cast ingots in a vacuum state, and the phosphorus content of the iron ingots is determined by chemical analysis. The results are shown in Table 2. It can be seen that the basicity of slag has a significant impact on the dephosphorization effect of molten iron. W
Embodiment 2
[0093] The iron ingot with a phosphorus content of 0.0016% in Example 1 was melted in a vacuum induction furnace. After the melting was complete, argon was used as a carrier gas to spray metal sodium particles into the molten iron for deoxidation and desulfurization. The injected Na and iron The molar ratio of O in water is 1.0-1.2, the flow rate of argon gas is 6.5L / min, and the duration is 1min; among them, metal Na is added at one time at the initial stage, and the molten iron is stirred by stirring components. The molten iron was ingot-cast in a vacuum state, and the oxygen and sulfur contents were determined by chemical analysis. The results are shown in Table 3. It can be seen that when the Na / O ratio is controlled above 1.05, the oxygen and sulfur contents of the molten iron are all lower than 10ppm, and When the Na / O ratio exceeds 1.1, the oxygen and sulfur contents of molten iron hardly change. In order to reduce the consumption of metal Na, the Na / O ratio prefera
Embodiment 3
[0097] Melt the iron ingot with the Na / O ratio of 1.1 to remove oxygen and sulfur in the vacuum induction furnace in Example 2. After the melting is complete, continue to spray Ar as a stirring gas to promote the removal of N and H gas impurities in the molten iron , and use the stirring parts to stir the molten iron; the time to continue spraying Ar is 5-20 minutes, and the molten iron after degassing is vacuum cast and chemically analyzed to measure the nitrogen and hydrogen content. The results are shown in Table 4. It can be seen that, When the argon blowing and stirring time is more than 10 minutes, the nitrogen and hydrogen contents of molten iron are lower than 4ppm. Since the nitrogen and hydrogen contents change little after the argon blowing and stirring time exceeds 15 minutes, in order to ensure the processing efficiency and reduce the consumption of argon, the present invention Preferably, the argon blowing stirring time is 10-15 minutes.
[0098] Table 4 Effect of
PUM
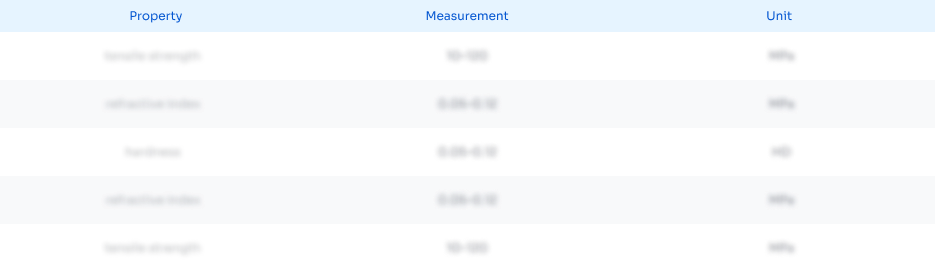
Abstract
Description
Claims
Application Information
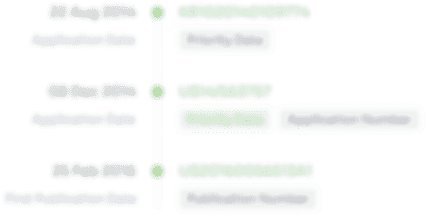
- R&D Engineer
- R&D Manager
- IP Professional
- Industry Leading Data Capabilities
- Powerful AI technology
- Patent DNA Extraction
Browse by: Latest US Patents, China's latest patents, Technical Efficacy Thesaurus, Application Domain, Technology Topic.
© 2024 PatSnap. All rights reserved.Legal|Privacy policy|Modern Slavery Act Transparency Statement|Sitemap