High-strength special-shaped channel steel and preparation method thereof
A special-shaped groove and high-strength technology, which is applied in the field of special channel steel, can solve the problems of affecting the corrosion resistance of channel steel, poor control of dosage, and affecting service strength, so as to achieve good slag formation, reduce inclusions, and improve serviceability. intensity effect
- Summary
- Abstract
- Description
- Claims
- Application Information
AI Technical Summary
Problems solved by technology
Method used
Examples
Embodiment 1
[0032] A high-strength special-shaped channel steel, the element composition of the channel steel and the weight percentage content of each component are: C: 0.25%; Si: 0.28%; Mn: 1.22%; P: 0.014%; S: 0.010%; V: 0.14%; Nb: 0.01%; AL: 0.025%; Cr: 0.10%; Cu: 0.25%;
Embodiment 2
[0034] A high-strength special-shaped channel steel, the element composition of the channel steel and the weight percentage content of each component are: C: 0.28%; Si≤0.19%; Mn: 1.11%; P: 0.016%; S: 0.009%; V: 0.12%; Nb: 0.06%; AL: 2.50%; Cr: 0.27%; Cu: 0.10%;
Embodiment 3
[0036] A high-strength special-shaped channel steel, the element composition of the channel steel and the weight percentage content of each component are: C: 0.24%; Si: 0.20%; Mn: 1.29%; P: 0.024%; S: 0.019%; V: 0.10%; Nb: 0.02%; AL: 4.30%; Cr: 0.09%; Cu: 0.20%;
[0037] A preparation method of high-strength special-shaped channel steel, comprising the following steps:
[0038] a. The molten iron is pre-desulfurized, and the sulfur content in the molten iron after desulfurization is controlled not to exceed 0.022wt%;
[0039] b. Smelting
[0040] All metal materials should meet the quality standards and be used after baking according to the system.
[0041] c. Refining
[0042] The molten steel in the primary furnace is fed into the furnace. During the refining process, the slag is fully stirred to form white slag or yellow-white slag. During the refining period, the molten steel temperature is controlled at 1640±10℃.
[0043] d. Electroslag remelting
[0044] The surface de
PUM
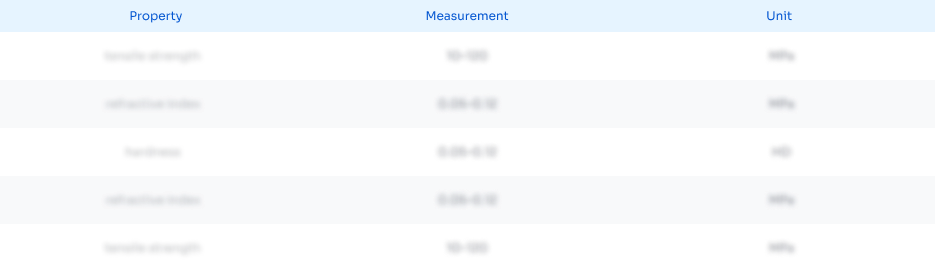
Abstract
Description
Claims
Application Information
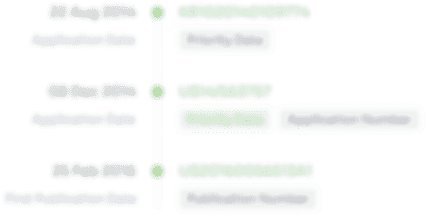
- R&D Engineer
- R&D Manager
- IP Professional
- Industry Leading Data Capabilities
- Powerful AI technology
- Patent DNA Extraction
Browse by: Latest US Patents, China's latest patents, Technical Efficacy Thesaurus, Application Domain, Technology Topic.
© 2024 PatSnap. All rights reserved.Legal|Privacy policy|Modern Slavery Act Transparency Statement|Sitemap