Matrix for MALDI analysis based on porous polymer monoliths
a porous polymer monolith and matrix technology, applied in the field of matrix, can solve the problems of preventing the use of maldi to analyze compounds that will decompose, interference of matrix ions with the ions of interest, and acidity of the matrix
- Summary
- Abstract
- Description
- Claims
- Application Information
AI Technical Summary
Benefits of technology
Problems solved by technology
Method used
Image
Examples
example 1
Preparation of the Monolithic Matrix via UV Initiated Polymerization
[0070] Described herein is the preparation of hydrophobic porous polymer in a format of well-defined monoliths located on a typical stainless steel MALDI plate and its use as a matrix for surface enhanced laser desorption / ionization of small molecules.
[0071] A mixture consisting of 24% butyl methacrylate, 16% ethylene dimethacrylate, 20,1% 1-decanol, and 39.9% cyclohexanol in which 2,2-dimethoxy-2-phenylacetophenone (1% with respect to monomers) was dissolved and used for the preparation of monolithic spots via UV initiated polymerization. A small volume of the polymerization mixture was placed on the top of a stainless steel plate (Applied Biosystems, Foster City, Calif.) and covered with a 1.1 mm thick and 100 mm diameter borofloat glass wafer (Precision Glass & Optics, Santa Ana, Calif.). The mask consisted of 100 circular spots with a diameter of 3 mm. The rows and columns of the mask were labeled with numbers
example 2
Preparation of the Monolithic Matrices via UV Initiated Polymerization
[0073] Using method described in Example 1 and polymerization mixtures shown in Table 1, series of monolithic spots for MALDI TOF MS differing in porous properties were obtained and are labeled in columns corresponding to polymerization mixtures A through D. Table 1 below shows the polymerization mixtures, reaction conditions and porous properties of each monolithic matrix prepared from each polymerization mixtures.
TABLE 1Polymerization MixtureABCDEethylene dimethacrylate, wt %1616161616butyl methacrylate, wt %24242424—benzyl methacrylate, wt %————241-decanol, wt %20.135.043.36060cyclohexanol, wt %39.925.016.7——2,2-dimehoxy-2-11111phenylacetophenoneapore volume, mL / g1.031.731.791.942.37median pore diameter, nm7020096021301204porosity, %5363605871specific surface area, m2 / g1106985—
aAmount of initiator with respect to monomers.
example 3
Preparation of the Monolithic Matrix via Thermal Polymerization.
[0074] Monolithic matrices were also prepared via thermally initiated polymerization from a polymerization mixture consisting of 20% styrene, 20% divinyl benzene, 43% decanol and 17% toluene using 1% AEBN (with respect to monomers) as the initiator. Polymerization was carried out using a thermal initiation assembly comprised of a MAILDI plate covered with a perforated polyethylene film that also acted as a sealing gasket. The polymerization mixture was spotted in the perforations of the film which acted as a mold to shape each monolith, on top of which was placed a heated aluminum plate which temperature was held at 80° C. Polymerization was allowed to proceed for 24 h, the mold was disassembled, and the plate surface with the attached monoliths washed with methanol. After the initial rinsing, all plates were placed in a beaker, covered with methanol, let stay overnight to extract the porogens, and dried in a vacuum oven
PUM
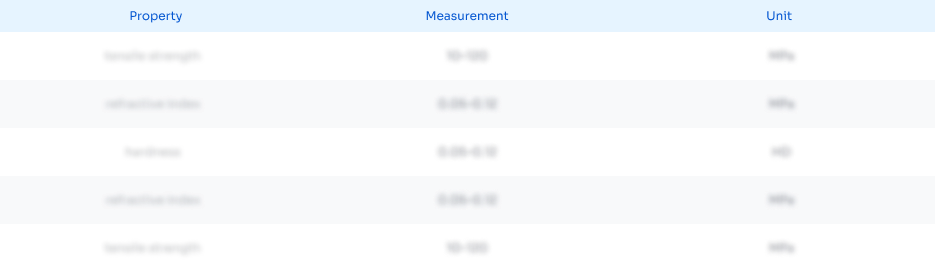
Abstract
Description
Claims
Application Information
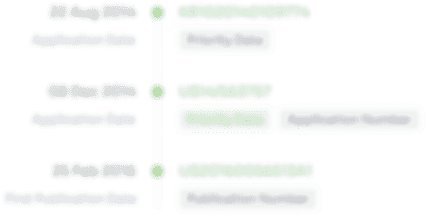
- R&D Engineer
- R&D Manager
- IP Professional
- Industry Leading Data Capabilities
- Powerful AI technology
- Patent DNA Extraction
Browse by: Latest US Patents, China's latest patents, Technical Efficacy Thesaurus, Application Domain, Technology Topic.
© 2024 PatSnap. All rights reserved.Legal|Privacy policy|Modern Slavery Act Transparency Statement|Sitemap