Chemical-Mechanical Polishing Compositions Containing Aspartame And Methods Of Making And Using The Same
a technology of compositions and polishing methods, applied in the field of compositions and compositions of chemical mechanical polishing and methods of making and using the same, can solve the problems of reducing the manufacturing throughput of shallow trench isolation structures, affecting the removal rate of silicon nitride, and severe topography variations, and achieve the effect of maintaining the extremely low silicon nitride ra
- Summary
- Abstract
- Description
- Claims
- Application Information
AI Technical Summary
Benefits of technology
Problems solved by technology
Method used
Image
Examples
example 1
[0027]CMP Slurry Compositions A1, A2 and A3 were prepared as shown in weight percent in Table 1 below.
TABLE 1SlurryCeO2AspartameDI-H2OpHA11% 0% 99%4.32A21%0.3%98.7%4.32A31%0.5%98.5%4.32
[0028]The “CeO2” used in each CMP Slurry Composition was a calcined cerium oxide derived from a cerium carbonate precursor that had a Dmean secondary particle size of 140 nm. A quantity of HNO3 was added to each CMP Slurry Composition sufficient to adjust the pH to 4.32. CMP Slurry Composition A1 was a control in that it did not contain any Aspartame.
[0029]CMP Slurry Compositions A1, A2 and A3 were separately used to polish blanket thermally grown silicon dioxide (“TOX”) and silicon nitride wafers (“Nitride”). The polisher used in each case was an Applied Materials Mirra system. For all test runs, the polishing conditions were 3.0 psi membrane pressure, 3.5 psi retaining ring pressure, 3.0 psi inner tube pressure, 93 rpm head speed and 87 rpm table speed. The flow rate of the CMP Slurry Compositions wa
example 2
[0031]CMP Slurry Compositions B1, B2 and B3 were prepared as shown in weight percent in Table 3 below.
TABLE 3SlurryCeO2AspartameDI-H2OpHB13% 0% 97%4.04B23%0.3%96.7%4.04B33%0.5%96.5%4.04
[0032]The “CeO2” used in each CMP Slurry Composition was the same as used in Example 1. A quantity of HNO3 was added to each CMP Slurry Composition sufficient to adjust the pH to 4.04. CMP Slurry Composition B1 was a control in that it did not contain any Aspartame.
[0033]CMP Slurry Compositions B1, B2 and B3 were separately used to polish blanket thermally grown silicon dioxide and silicon nitride wafers using the equipment and polishing conditions described in Example 1. The removal rate of each material in Å / min and silicon dioxide to silicon nitride selectivity is set forth in Table 4:
TABLE 4SlurryTOX RRNitride RRSelectivityB11936.91439.11B22852.418.0158B32562.210.9235
[0034]Example 2 shows that at 3% ceria and at pH of about 4.0, the selectivity increases with Aspartame additions and even has an i
example 3
[0035]CMP Slurry Compositions C1, C2 and C3 were prepared as shown in weight percent in Table 5 below.
TABLE 5SlurryCeO2AspartameWaterpHC110993.9C210.198.94.4C310.498.64.0
[0036]The “CeO2” used in each CMP Slurry Composition was the same as used in Example 1. CMP Slurry Composition C1 was a control in that it did not contain any Aspartame.
[0037]CMP Slurry Compositions C1, C2 and C3 were separately used to polish patterned high density plasma (HDP) silicon dioxide films using the equipment and polishing conditions described in Example 1. The amount of up area removed (active removal rate, ACT Removed) of each material removed in Å for different polish times is set forth in Table 6 and further illustrated in FIG. 1:
TABLE 6C1C2C3TimeACT RemovedACT RemovedACT Removed000060840130916427511023919245490139445375019105164457565962
[0038]Example 3 shows that at 1% ceria and at a pH of about 4.0, the silicon dioxide step height removal rate is increased with Aspartame additions.
PUM
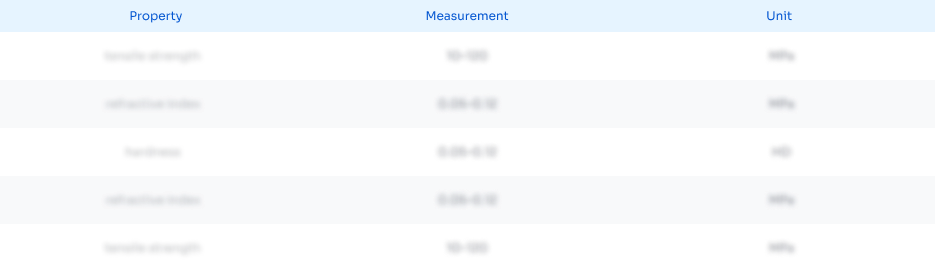
Abstract
Description
Claims
Application Information
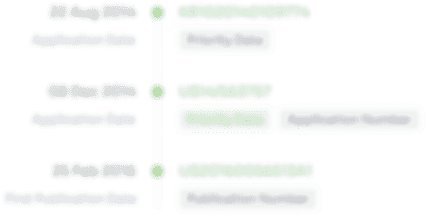
- R&D Engineer
- R&D Manager
- IP Professional
- Industry Leading Data Capabilities
- Powerful AI technology
- Patent DNA Extraction
Browse by: Latest US Patents, China's latest patents, Technical Efficacy Thesaurus, Application Domain, Technology Topic.
© 2024 PatSnap. All rights reserved.Legal|Privacy policy|Modern Slavery Act Transparency Statement|Sitemap