Technique and process for controlling material properties during impact consolidation of powders
- Summary
- Abstract
- Description
- Claims
- Application Information
AI Technical Summary
Benefits of technology
Problems solved by technology
Method used
Examples
Example
Example 1
[0050]FIG. 4 shows a light micrograph coating cross-section of commercially pure titanium [(CP-Ti)-325 mesh] powder deposited with an impact consolidation process using the friction compensated sonic nozzle disclosed in U.S. Pat. No. 6,915,964 issued to Tapphorn and Gabel. This −325 mesh CP-Ti powder was deposited on an aluminum alloy substrate to a total thickness of approximately 4.4-mm using helium gas at a nozzle inlet pressure of 105-psia and nozzle temperature of approximately 600° F. The deposition efficiency for this −325 mesh CP-Ti powder is approximately 77%.
[0051]Note the high degree of porosity (8% by volume) occurring throughout the interior bulk region of the CP-Ti coating with a surface porosity as high as 27% extending 0.8-mm below the surface to the coating. Additionally the coating exhibits an interface porosity of approximately 12% near the aluminum alloy substrate.
[0052]In contrast, FIG. 5 shows a light micrograph coating cross section of commercially pure
Example
Example 2
[0060]A second example of using the embodiment described with FIG. 1, was evaluated using commercially pure aluminum powder (CP-Al) having a particle size distribution of −140 to +325 mesh. The powder was initially deposited with an impact consolidation process using the friction compensated sonic nozzle disclosed in U.S. Pat. No. 6,915,964 issued to Tapphorn and Gabel. This CP-Al powder was deposited on an aluminum alloy substrate to a total thickness of approximately 4.2-mm using helium gas at a nozzle inlet pressure of 105-psia and nozzle temperature of approximately 600° F. The deposition efficiency for this CP-Al powder is approximately 15% which is low for aluminum powders, but was selected as a coarse aluminum powder example with a relatively high porosity when deposited using the impact consolidation process unique to the friction compensated sonic nozzle disclosed in U.S. Pat. No. 6,915,964 issued to Tapphorn and Gabel operating at relative low input pressures.
[0061]F
PUM
Property | Measurement | Unit |
---|---|---|
Density | aaaaa | aaaaa |
Stress optical coefficient | aaaaa | aaaaa |
Abstract
Description
Claims
Application Information
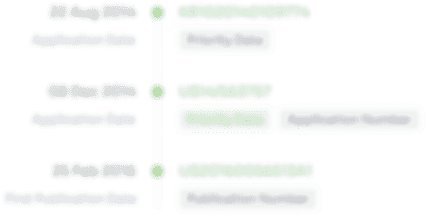
- R&D Engineer
- R&D Manager
- IP Professional
- Industry Leading Data Capabilities
- Powerful AI technology
- Patent DNA Extraction
Browse by: Latest US Patents, China's latest patents, Technical Efficacy Thesaurus, Application Domain, Technology Topic.
© 2024 PatSnap. All rights reserved.Legal|Privacy policy|Modern Slavery Act Transparency Statement|Sitemap