High temperature thermal energy storage system
a technology of thermal energy storage and high temperature, which is applied in the direction of indirect heat exchangers, machines/engines, light and heating equipment, etc., can solve the problems of fracture and gravelization of the pcm
- Summary
- Abstract
- Description
- Claims
- Application Information
AI Technical Summary
Benefits of technology
Problems solved by technology
Method used
Image
Examples
Embodiment Construction
[0018]Referring now to the drawings, in which like numerals indicate like elements throughout the several views, FIG. 1 depicts one embodiment of the helically grooved tube-capsules 104. The capsules may be formed from a thin wall metal tube by enrolling helical grooves along the length of the tubes or by extrusion or other metal forming procedure. The grooved tubes may resemble the rifled barrel of guns. The ratio of the length to the diameter of the tube is from 6 to 300. The angle 107 between the tangent of the helix of the grooves and the axis of the tube may be from 0 to 30 degrees. The shape of the profile of the groove 105 is curved that may be circular or oval. The number of the grooves on the tube may be from 2 to 12. The ratio of the depth of the groove to the diameter of the tube may be from 0.02 to 0.4. The purpose of the grooving is to provide radial and axial flexibility of the tube wall to accommodate the thermal expansion of the encapsulated phase change material. At th
PUM
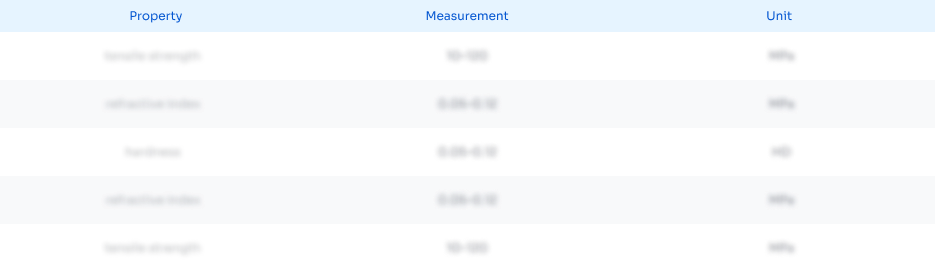
Abstract
Description
Claims
Application Information
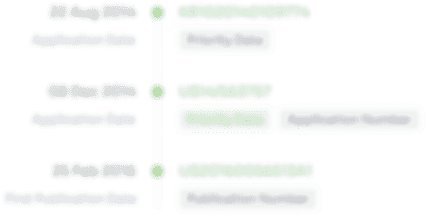
- R&D Engineer
- R&D Manager
- IP Professional
- Industry Leading Data Capabilities
- Powerful AI technology
- Patent DNA Extraction
Browse by: Latest US Patents, China's latest patents, Technical Efficacy Thesaurus, Application Domain, Technology Topic.
© 2024 PatSnap. All rights reserved.Legal|Privacy policy|Modern Slavery Act Transparency Statement|Sitemap