Toner and two-component developer
a two-component developer and toner technology, applied in the field of toner and two-component developers, can solve the problems of high dispersibility and difficulty in satisfying both, and achieve the effects of high fixability, high hot offset resistance, and high durability
- Summary
- Abstract
- Description
- Claims
- Application Information
AI Technical Summary
Benefits of technology
Problems solved by technology
Method used
Image
Examples
examples
[0177]The application will be further described in detail with reference to Examples, which are not intended to limit the embodiments of the application. The term “part(s)” used hereinafter refers to “part(s) by mass”. Before the description of Examples, preparation examples of amorphous polyester resin A, additive C and crystalline polyester resin D will be described.
preparation example a-1
[0178]The raw material monomers in the proportions (on a mole basis) shown in Table 1 were added into a reaction vessel equipped with a nitrogen inlet, a dehydration tube, a stirrer and a thermocouple, and 1.5 parts by mass of dibutyl tin was added relative to the total mass (100 parts by mass) of the raw material monomers. Then, the temperature in the vessel was increased to 160° C. with stirring in a nitrogen atmosphere.
[0179]Then, the mixture in the vessel was polycondensated while water was removed by heating the mixture from 160° C. to 200° C. at a heating rate of 10° C. / h with stirring. After the inner temperature of the reaction vessel reached 200° C., the vessel was evacuated to 5 kPa or less, and polycondensation was performed under the conditions of 200° C. and 5 kPa or less. The reaction product taken out from the reaction vessel was cooled and pulverized to yield amorphous polyester resin A-1. The physical properties of the resulting amorphous polyester resin A-1 are show
preparation example a-2
[0181]The raw material monomers in the proportions (on a mole basis) shown in Table 1 were added into a reaction vessel equipped with a nitrogen inlet, a dehydration tube, a stirrer and a thermocouple, and 1.5 parts by mass of dibutyl tin was added relative to the total mass (100 parts by mass) of the raw material monomers. Then, the temperature in the vessel was increased to 180° C. with stirring in a nitrogen atmosphere. Then, the mixture in the vessel was polycondensated under normal pressure in a nitrogen atmosphere while water was removed by heating the mixture from 180° C. to 230° C. at a heating rate of 10° C. / h with stirring.
[0182]After the inner temperature of the reaction vessel reached 230° C., the vessel was evacuated to 5 kPa or less, and polycondensation was performed under the conditions of 230° C. and 5 kPa or less. The reaction product taken out from the reaction vessel was cooled and pulverized to yield amorphous polyester resin A-2. The physical properties of the r
PUM
Property | Measurement | Unit |
---|---|---|
Temperature | aaaaa | aaaaa |
Temperature | aaaaa | aaaaa |
Temperature | aaaaa | aaaaa |
Abstract
Description
Claims
Application Information
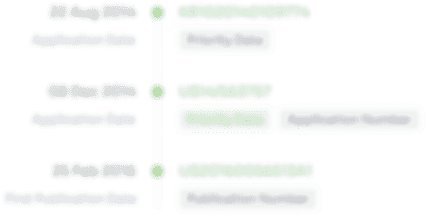
- R&D Engineer
- R&D Manager
- IP Professional
- Industry Leading Data Capabilities
- Powerful AI technology
- Patent DNA Extraction
Browse by: Latest US Patents, China's latest patents, Technical Efficacy Thesaurus, Application Domain, Technology Topic.
© 2024 PatSnap. All rights reserved.Legal|Privacy policy|Modern Slavery Act Transparency Statement|Sitemap