Dual clutch gearbox with countershaft design
- Summary
- Abstract
- Description
- Claims
- Application Information
AI Technical Summary
Benefits of technology
Problems solved by technology
Method used
Image
Examples
Embodiment Construction
[0031]The structure of dual-clutch transmissions of countershaft design is already well known to those with knowledge of the subject, so that in the figure descriptions only the components relevant to the invention will be described and explained in detail. The same indexes are used for the same components.
[0032]FIG. 1 shows a dual-clutch transmission 9 of countershaft design, comprising a main transmission 10 and a group transmission 11 connected downstream from the main transmission 10, wherein the main transmission 10 comprises a first transmission input shaft EW1 in the form of a solid shaft connected to the drive output side of a first powershiftable clutch K1 which is associated with a first partial transmission, and a second transmission input shaft EW2 in the form of a hollow shaft connected to the drive output side of a second powershiftable clutch K2, through which shaft the first transmission input shaft EW1 passes, and which is associated with a second partial transmission,
PUM
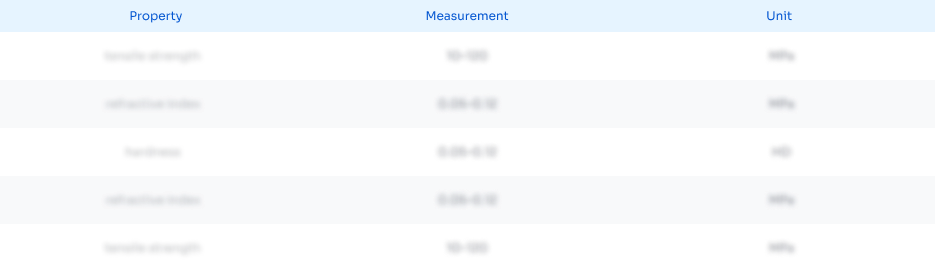
Abstract
Description
Claims
Application Information
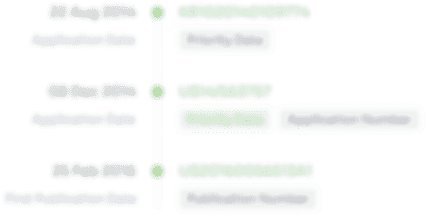
- R&D Engineer
- R&D Manager
- IP Professional
- Industry Leading Data Capabilities
- Powerful AI technology
- Patent DNA Extraction
Browse by: Latest US Patents, China's latest patents, Technical Efficacy Thesaurus, Application Domain, Technology Topic.
© 2024 PatSnap. All rights reserved.Legal|Privacy policy|Modern Slavery Act Transparency Statement|Sitemap