Active composite variable damping rotational control device
a control device and composite variable technology, applied in the direction of spring/damper functional characteristics, shock absorption, shock proofing, etc., can solve the problems of low control efficiency, almost useless to control the torsional swing, and weakening the control effect and even completely losing the function, etc., to achieve greater robustness
- Summary
- Abstract
- Description
- Claims
- Application Information
AI Technical Summary
Benefits of technology
Problems solved by technology
Method used
Image
Examples
Embodiment Construction
[0027]The present invention is further described below in combination with the accompanying drawings.
[0028]In the present embodiment, a structure with a simple pendulum structure model as a basic mechanical model prototype is taken as an example.
[0029]As shown in FIGS. 1-3, an active composite variable damping rotational control device of the present invention includes a variable damping module 100 and a power module 200. The variable damping module 100 includes a magnetorheological fluid tank 1 and a rotational inertia wheel 2. The power module 200 includes a device tubular cavity 3, and a driver 4, an encoder 5 and a speed changer 6 which are fixed in the device tubular cavity 3. The device tubular cavity 3 is connected with a controlled structure 7. The rotational inertia wheel 2 is parallel to a surface of the controlled structure 7 that is subjected to the torsional swing.
[0030]The magnetorheological fluid tank 1 is a round tubular shape. Two circular end surfaces 1.1 and a cylind
PUM
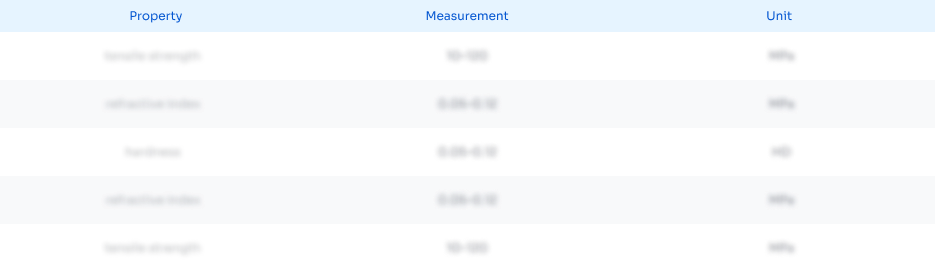
Abstract
Description
Claims
Application Information
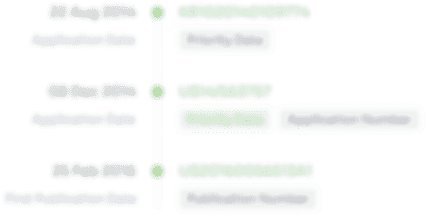
- R&D Engineer
- R&D Manager
- IP Professional
- Industry Leading Data Capabilities
- Powerful AI technology
- Patent DNA Extraction
Browse by: Latest US Patents, China's latest patents, Technical Efficacy Thesaurus, Application Domain, Technology Topic.
© 2024 PatSnap. All rights reserved.Legal|Privacy policy|Modern Slavery Act Transparency Statement|Sitemap