Coal tar compositions modified by nitrile butadiene rubber
- Summary
- Abstract
- Description
- Claims
- Application Information
AI Technical Summary
Benefits of technology
Problems solved by technology
Method used
Examples
example 2
The same procedure, NBR rubber and coal tar pitch as in Example 1 were used for Example 2. However, a plasticizer, specifically, di-octyl adipate ("DOA"), commercially available from Harwick Chemical of Akron, Ohio, was added immediately following the charge of coal tar at three different levels to determine the benefit thereof. The levels of DOA addition are designated as experiments 2A through 2C, as shown in Table 3:
The resulting compositions were tested similarly to the compositions in Example 1, although additional tests were conducted for low temperature flexibility using different mandrel and specimen sizes. "Flexibility 1" below refers to the same one-inch mandrel and one-inch by six-inches by 0.1-inch specimen. In "Flexibility 2", a 0.5-inch mandrel was used and a 0.5-inch by three-inch by 0.05-inch specimen was used. Also, a recovery from 300% elongation test was used because the elongation tests were so successful, and is reported below as "Recovery". Table 4 shows the resul
example 3
The Example 3 experiments were intended to measure the efficacy of different plasticizers or process oils, at the same level of the di-octyl adipate addition in experiment 2A, that is, 5 parts by weight of plasticizer per 90 parts by weight of coal tar pitch and 5 parts per weight of NBR. The same procedure, NBR rubber and coal tar pitch as in Example 1 were used. In experiment 3A, the plasticizer used was di-octyl phthalate, obtained from Harwick Chemical in Akron, Ohio. In experiment 3B, the plasticizer was HERCOFLEX 600, a high-boiling monomeric ester from Hercules, Inc., of Wilmington, Del. In experiment 3C, the plasticizer used was PLASTHALL 7050, a monomeric di-ester produced by The C.P. Hall Company of Stow, Ohio. In experiment 3D, the plasticizer was VIPLEX 525, a heavy refined naphthenic oil from Crowley Chemical of New York, N.Y. Low temperature flexibility in this case was tested using the one-inch mandrel and with a one-inch by six-inch by 0.1-inch specimen, as in Example 1
example 4
In Example 4, an RT-12 grade refined coal tar was substituted for the Type I coal tar pitch which had been used in Example 1. This RT-12 coal tar may be characterized as being softer, less viscous and having more low end coal tar fractions than the Type I coal tar pitch. The RT-12 coal tar was charged to a heated mixing vessel and allowed to thermally equilibrate in the range of 350 to 375.degree. F. A charge of a linear NBR having a 33% acrylonitrile content in powder form and dusted with a calcium carbonate partitioning agent was used for the experiments of Example 1. The NBR is commercially available from Goodyear Chemical and is sold under the tradename CHEMIGUM P609. It typically has a Mooney viscosity of 85, and the CaCO.sub.3 partitioning agent is present at about 9% by weight. The polymer charge was added in even increments and dispersed through the use of a high speed paddle-type mixer. The specific mixer used was an air-driven Fawcett Model 103A. The blend was mixed for 60 mi
PUM
Property | Measurement | Unit |
---|---|---|
Percent by mass | aaaaa | aaaaa |
Percent by mass | aaaaa | aaaaa |
Percent by mass | aaaaa | aaaaa |
Abstract
Description
Claims
Application Information
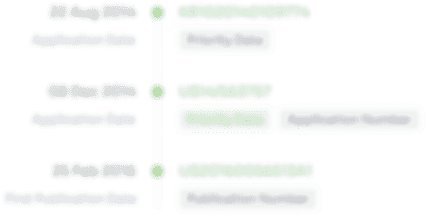
- R&D Engineer
- R&D Manager
- IP Professional
- Industry Leading Data Capabilities
- Powerful AI technology
- Patent DNA Extraction
Browse by: Latest US Patents, China's latest patents, Technical Efficacy Thesaurus, Application Domain, Technology Topic.
© 2024 PatSnap. All rights reserved.Legal|Privacy policy|Modern Slavery Act Transparency Statement|Sitemap