Method for making molecular sieves and novel molecular sieve compositions
a technology of molecular sieves and compositions, applied in the direction of silicates, physical/chemical process catalysts, silicon compounds, etc., can solve the problems of framework degrade and no longer be able to provide the macro and mesopore network
- Summary
- Abstract
- Description
- Claims
- Application Information
AI Technical Summary
Benefits of technology
Problems solved by technology
Method used
Examples
example 2
Conversion to zeolite beta Shell.RTM. (S 980 A 3.0) 3.0 mm silica spheres (3.09 grams) were fully impregnated to incipient wetness by a mixture of 1.25 grams of Al(NO.sub.3).sub.3.9H.sub.2 O dissolved in 6.00 grams of water to obtain a Si / Al ratio of 15 in the impregnated product. The impregnated product was air dried at 120.degree. C. to a constant weight. Two grams of these impregnated spheres were additionally impregnated with an aqueous 35 weight % tetraethylammonium hydroxide solution and 1.04 grams of an aqueous 3.68 weight % NANO.sub.3 solution, giving a molar oxide ratio of
13.3 SiO.sub.2 O:0.43 Al.sub.2 O.sub.3 :1 TEA.sub.2 O:0.1 Na.sub.2 O: 55 H.sub.2 O
The mixture was placed in a 30 ml stainless steel autoclave with a 25 ml Teflon.RTM. insert. After heating for 44 hours at 155.degree. C., the product possessed 82% zeolite beta crystals and the morphology of the Shell 3.0 mm silica spheres.
example 3
Conversion to zeolite beta Davison.RTM. Sylopol.RTM. 948 silica gel 50 .mu.m spheres were air-milled to a particle size of 3-5 .mu.m. Then 3.10 grams of the milled particles were fully impregnated to incipient wetness by a mixture of 1.25 grams of Al(NO.sub.3).sub.3 and 10.0 grams of water to result in a Si / Al ratio of 15, and then dried in air at 120.degree. C. to a constant weight. Two and one-half grams of the milled and impregnated particles were impregnated with 2.50 grams of an 35 weight % aqueous tetraethylammonium hydroxide solution and 1.25 grams of an 3.68 weight % aqueous NaNO.sub.3 solution, resulting in a molar oxide ratio of
13.2 SiO.sub.2 :0.44 Al.sub.2 O.sub.3 :1.00 TEA.sub.2 O:0.1Na.sub.2 O:55 H.sub.2 O
The mixture was placed in a 35 ml stainless steel autoclave with a 10 ml Teflon.RTM. insert. After 46 hours at 155.degree. C., the powder had been converted to 47 weight % zeolite beta. After ultrasonic treatment for 3 hours, the individual particle size of 3-5 .mu.m wa
example 4
Conversion to zeolite beta As described in Example 1 above, 3.10 grams of Davison.RTM. Sylopol.RTM. 948 silica gel 50 .mu.m spheres were fully impregnated to incipient wetness by a solution made from 1.26 grams of Al(NO.sub.3).sub.3.9H.sub.2 O and 8.60 grams of water, dried in air at 120.degree. C. and calcined at 400.degree. C. for 3 hours, cooled to room temperature and calcined at 800.degree. C. for 3 hours, resulting in 5.35 weight % Al.sub.2 O, content (Si / Al ratio is 15).
Two and one-half grams (2.50 grams) of these spheres were impregnated with 2.50 grams of an aqueous 35 weight % tetraethylammonium hydroxide solution and 1.25 grams of an aqueous 3.68 weight % NaNO.sub.3 solution. The molar oxide ratio was:
13.2 SiO.sub.2 :0.44 Al.sub.2 O.sub.3 :1.00 TEA.sub.2 O: 0.10Na.sub.2 O:55 H.sub.2 O
The mixture was placed in a 35 ml stainless steel autoclave with a 10 ml Teflon.RTM. insert. After 44 hours at 160.degree. C., the spheres were converted to 94 weight % zeolite beta According
PUM
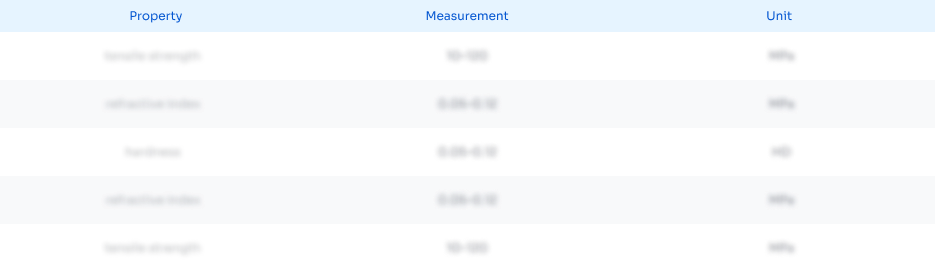
Abstract
Description
Claims
Application Information
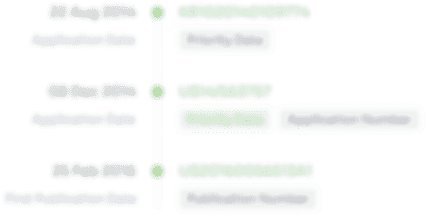
- R&D Engineer
- R&D Manager
- IP Professional
- Industry Leading Data Capabilities
- Powerful AI technology
- Patent DNA Extraction
Browse by: Latest US Patents, China's latest patents, Technical Efficacy Thesaurus, Application Domain, Technology Topic.
© 2024 PatSnap. All rights reserved.Legal|Privacy policy|Modern Slavery Act Transparency Statement|Sitemap