Double-component modification method of molecular sieve in FCC catalyst and molecular sieve modified through method
A molecular sieve and two-component technology, applied in molecular sieve catalysts, chemical instruments and methods, physical/chemical process catalysts, etc., can solve the problems of poor stability and activity of molecular sieves, decreased retention rate of modified elements, loss of phosphorus modified elements, etc. problems, to achieve good hydrothermal stability and catalytic activity, prevent a large amount of loss, and increase the effect of acid content
- Summary
- Abstract
- Description
- Claims
- Application Information
AI Technical Summary
Problems solved by technology
Method used
Image
Examples
Embodiment 1
[0057] Take 1.86 g (NH 4 ) 2 HPO 4 Dissolve in 100 grams of distilled water, add 20 grams of ZSM-5 molecular sieve sample into the solution under stirring condition, and adjust the pH value to 4. At a reaction temperature of 100°C, stirring and reacting for 60 minutes, it directly enters flash drying, and then the obtained sample is calcined at 500°C with 30% water vapor for 4 hours to obtain a molecular sieve. Take 0.73g of zirconium nitrate and dissolve it in 350g of distilled water, add a molecular sieve into the zirconium-containing solution, stir and react at a reaction temperature of 20°C for 120 minutes, then flash dry, then roast at 500°C for 2 hours, and the obtained The molecular sieve sample was designated NZ-1. Then kaolin (45%), aluminum sol (15%) and NZ-1 (40%) were added into distilled water for beating according to the above ratio, dried at 120°C, roasted at 450°C for 1 hour, crushed and sieved, and the obtained catalyst sample was recorded as CNZ -1. 20-40 m
Embodiment 2
[0059] Take 6.48 g H 3 PO 4 Dissolve in 80 grams of distilled water, add 20 grams of ZSM-5 molecular sieve sample into the solution under stirring conditions, and adjust the pH value to 1. At a reaction temperature of 160°C, stirring and reacting for 120 minutes, flash drying was carried out, and then calcined at 300°C for 6 hours to obtain a molecular sieve. Take 1.46g of titanium tetrachloride and dissolve it in 350g of distilled water, add a molecular sieve into the zirconium-containing solution, stir and react at a reaction temperature of 40°C for 100 minutes, perform flash drying, and then roast at 500°C for 2 hours , The resulting sample is denoted as NZ-2. Then kaolin (45%), aluminum sol (15%) and NZ-2 (40%) were added into distilled water in a fixed proportion for beating, dried at 120°C, roasted at 450°C for 1 hour, crushed and sieved, and the obtained catalyst sample was recorded as CNZ -2. Catalyst samples with 20-40 mesh particles were taken for microactivity inve
Embodiment 3
[0061] Take 1.80 g H 3 PO 4 Dissolve in 80 grams of distilled water, add 20 grams of ZSM-5 molecular sieve sample into the solution under stirring conditions, and adjust the pH value to 5. At a reaction temperature of 160°C, stir and react for 120 minutes to flash dry, and then bake at 500°C for 6 hours to obtain a molecular sieve. Dissolve 1.46g of ferric nitrate in 350g of distilled water, add a molecular sieve to the iron-containing solution, stir and react at a reaction temperature of 40°C for 100 minutes, then enter flash drying, and then roast at 500°C for 2 hours to obtain The sample is designated as NZ-3. Then kaolin (45%), aluminum sol (15%) and NZ-3 (40%) were added in proportion to beating in distilled water, dried at 120°C, roasted at 450°C for 1 hour, crushed and sieved, and the obtained catalyst sample was recorded as CNZ- 3. The composition of the molecular sieve samples, the crystallinity before and after aging and the microreactivity of the obtained catalyst
PUM
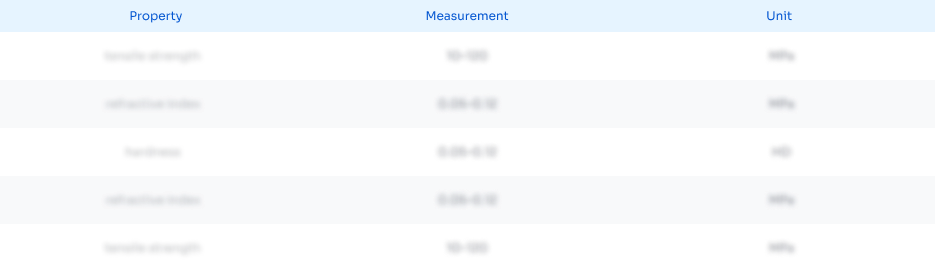
Abstract
Description
Claims
Application Information
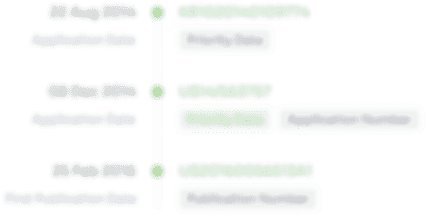
- R&D Engineer
- R&D Manager
- IP Professional
- Industry Leading Data Capabilities
- Powerful AI technology
- Patent DNA Extraction
Browse by: Latest US Patents, China's latest patents, Technical Efficacy Thesaurus, Application Domain, Technology Topic.
© 2024 PatSnap. All rights reserved.Legal|Privacy policy|Modern Slavery Act Transparency Statement|Sitemap