Method of Fabricating Thin Film by Microplasma Processing and Apparatus for Same
a technology of microplasma and processing method, which is applied in the direction of plasma technique, vacuum evaporation coating, coating, etc., can solve the problems of high inefficiency of methods, waste of raw materials, and inability to use gaseous raw materials harmful to human body or environment, and achieve high adhesion
- Summary
- Abstract
- Description
- Claims
- Application Information
AI Technical Summary
Benefits of technology
Problems solved by technology
Method used
Examples
Embodiment Construction
[0088]Embodiments of the present invention are now explained in detail with reference to the attached drawings. The following embodiments are merely for facilitating the understanding of this invention, and the present invention shall in no way be limited thereby. In other words, various modifications and other embodiments based on the technical spirit of the present invention shall be included in this invention as a matter of course.
(Explanation of Atmospheric-Pressure Plasma Thin-Film Fabrication Apparatus)
[0089]FIG. 1 is a view showing a frame format of the configuration of the plasma generator pertaining to the present embodiment and the connection method to the gas pipe. The plasma generator is configured from an alumina narrow tube 1, and a metal tube 2 for supporting the alumina narrow tube. The end of a raw material wire 3 inserted into the narrow tube is fixed to the inner wall of the metal tube 2 for supporting the narrow tube. The plasma generator is connected to a gas fe...
PUM
Property | Measurement | Unit |
---|---|---|
diameter | aaaaa | aaaaa |
diameter | aaaaa | aaaaa |
inner diameter | aaaaa | aaaaa |
Abstract
Description
Claims
Application Information
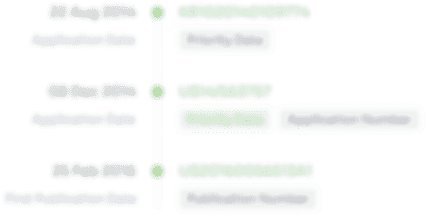
- R&D Engineer
- R&D Manager
- IP Professional
- Industry Leading Data Capabilities
- Powerful AI technology
- Patent DNA Extraction
Browse by: Latest US Patents, China's latest patents, Technical Efficacy Thesaurus, Application Domain, Technology Topic.
© 2024 PatSnap. All rights reserved.Legal|Privacy policy|Modern Slavery Act Transparency Statement|Sitemap