Special pressure for industrial detonating cap and method for compressing detonating cap explosive
A press and detonator technology, applied in the field of press manufacturing, can solve the problems that are not conducive to the use of automatic detonator filling lines, large basic investment in hydraulic pump stations, and large volume of hydraulic presses, etc., to achieve convenient automatic control, low equipment cost, and basic investment Reduced effect
- Summary
- Abstract
- Description
- Claims
- Application Information
AI Technical Summary
Benefits of technology
Problems solved by technology
Method used
Image
Examples
Embodiment 1
[0009] Embodiment 1: with reference to accompanying drawing 1. The special pressing machine for industrial detonators comprises a frame 8 and is manufactured according to the prior art with reference to accompanying drawing 1 . The four columns 3 refer to columns with column covers, the four columns 3 are respectively positioned at (installed on) the side of the frame 8 and the lower ends of the four columns are connected with the lifting plate 6, and the tops of the four columns are connected with the hydraulic compensation head 2 The hydraulic compensation head 2 is composed of a hydraulic compensator 1 and a plurality of hydraulic plungers 11. The plurality of hydraulic plungers 11 are respectively located in the hydraulic lifting chamber of the hydraulic compensator 1 and protrude together under the state of hydraulic pressure. Retracts in hydraulically unloaded state. The pressurization (loading) or unloading of the hydraulic compensation head 2 depends on the gas-hydraulic
Embodiment 2
[0010] Embodiment 2: On the basis of Embodiment 1, the method for compressing the detonator explosives with a special press for industrial detonators is to send the turnover mold with fire detonators into the positioning seat of the turnover mold of the special press for industrial detonators, and the piston in the main cylinder pushes The lifting plate moves down, and the multiple plungers in the hydraulic compensation head drop from the top dead center to the drug surface in the tube shell. The self-locking rod in the self-locking mechanism is pushed to the vertical state by the cylinder and locks the four-column lifting mechanism. The gas-hydraulic pressurization mechanism works to pressurize the hydraulic compensation head and directly acts on multiple plungers in the hydraulic compensation head. The plungers complete the compression of the explosives loaded in the detonator. When the compression reaches the set value, The gas-hydraulic booster mechanism is unloaded, the self-
PUM
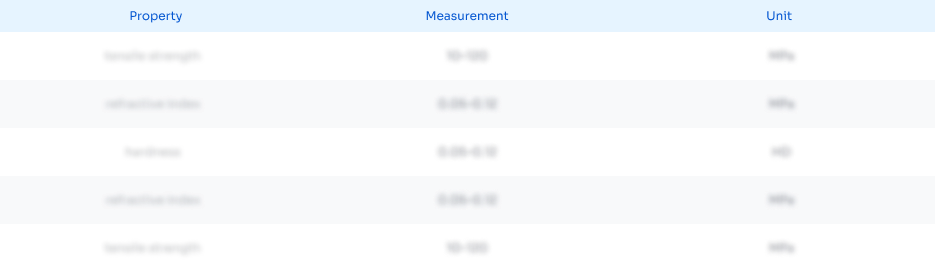
Abstract
Description
Claims
Application Information
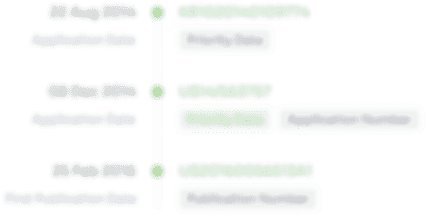
- R&D Engineer
- R&D Manager
- IP Professional
- Industry Leading Data Capabilities
- Powerful AI technology
- Patent DNA Extraction
Browse by: Latest US Patents, China's latest patents, Technical Efficacy Thesaurus, Application Domain, Technology Topic.
© 2024 PatSnap. All rights reserved.Legal|Privacy policy|Modern Slavery Act Transparency Statement|Sitemap