Lower spraying and cooling device arranged between finishing mill frames
A cooling device and inter-stand technology, applied in metal rolling, metal rolling, metal processing equipment, etc., can solve problems such as uneven cooling distribution, reduce temperature drop, ensure plate shape, and avoid waste of resources.
- Summary
- Abstract
- Description
- Claims
- Application Information
AI Technical Summary
Benefits of technology
Problems solved by technology
Method used
Image
Examples
Embodiment 1
[0036] Such as Figure 2-Figure 5 As shown, the down spray cooling device between the finishing stands includes a header 1, which is arranged along the direction vertical to the running direction of the steel strip, and the water inlet pipe 11 is arranged on the header 1 and connected with it, and the central axis of the water inlet pipe 11 is connected with the There is an included angle between the horizontal central axes of the headers, and a number of discharge pipes are evenly distributed on it along the axial direction of the header 1, and each row of nozzles includes two nozzles 4, and the two nozzles 4 are arranged along the 1 Arranged in the radial direction, the two nozzle pipes 4 are connected to the header pipe 1 through their lower ends, and several sets of plunger devices 5 are respectively arranged corresponding to several nozzle discharge pipes. Wherein each set of plunger device 5 all comprises: plunger pipe 6 is correspondingly arranged under each row of spray p
Embodiment 2
[0039] Such as figure 2 , image 3 , Figure 6 and Figure 7 As shown, the downspray cooling device includes a header 1, the header 1 is arranged along the vertical running direction of the strip steel, the water inlet pipe 11 is arranged on the header 1 and communicates with it, and the central axis of the water inlet pipe 11 is horizontal to the header There is an included angle between the central axes, and a number of discharge pipes are evenly distributed on it along the axial direction of the header 1, and each row of nozzles includes two nozzles 4, and the two nozzles 4 are arranged along the radial direction of the header 1. Arranged in the same direction, the two nozzle pipes 4 are connected to the header pipe 1 through their lower ends, and several sets of plunger devices 5 are respectively arranged correspondingly to several nozzle discharge pipes. Wherein each set of plunger device 5 all comprises: plunger pipe 6 is correspondingly arranged under each row of spray
PUM
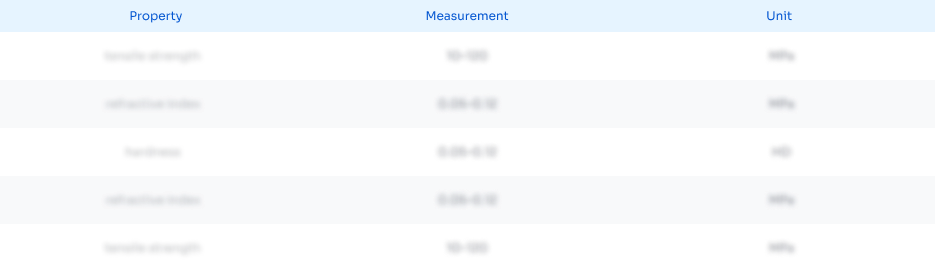
Abstract
Description
Claims
Application Information
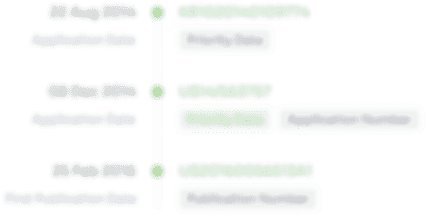
- R&D Engineer
- R&D Manager
- IP Professional
- Industry Leading Data Capabilities
- Powerful AI technology
- Patent DNA Extraction
Browse by: Latest US Patents, China's latest patents, Technical Efficacy Thesaurus, Application Domain, Technology Topic.
© 2024 PatSnap. All rights reserved.Legal|Privacy policy|Modern Slavery Act Transparency Statement|Sitemap