Biomass gasified tar processing system and method
A treatment system, biomass gas technology, applied in the direction of combustible gas purification, combustible gas purification/transformation, condensed non-gaseous material gas purification, etc., can solve the problems of pipeline blockage, tar affecting equipment use, etc., achieve efficiency improvement and easy implementation , large economic and social benefits
- Summary
- Abstract
- Description
- Claims
- Application Information
AI Technical Summary
Problems solved by technology
Method used
Examples
Example Embodiment
[0031] Example 1
[0032] Such as figure 1 As shown, the biomass gasification tar processing system includes a cyclone separator 1, a condenser 2, a spray washing tower 3, a charcoal adsorption tank 4, and an activated carbon adsorption tank 5.
[0033] The cyclone 1 is provided with a first biomass fuel gas inlet A and a first biomass fuel gas outlet 12, and an ash outlet C is provided at the bottom of the cyclone;
[0034] The condenser 2 is provided with a second biomass gas inlet 21, a second gas outlet 22, a cooling water inlet D, a water outlet E, and a first tar outlet 25. The first tar outlet 25 is connected to the tar storage chamber 6 through a pipeline, and the tar storage A heavy tar outlet G is provided at the bottom of the chamber 6, and a diving valve d is added to the pipeline of the heavy tar outlet. The condenser 2 is provided with a U-shaped tube 26, the bottom of the U-shaped tube is provided with a U-shaped tube bottom outlet 27, the upper end of the U-shaped tube
Example Embodiment
[0037] Example 2
[0038] First, biomass is gasified through a biomass fixed-bed gasifier (including air gasification, oxygen gasification, steam gasification, oxygen-steam mixed gasification, air-oxygen mixed gasification), and the gasified fuel gas is passed through The purification of this system includes the following steps:
[0039] 1) Before the system works, make sure that the intake valves a, b, c, e, f are open, and the d, g valves are closed;
[0040] 2) Biomass gasification fuel gas A first passes through cyclone separator 1 of this system for dust removal and a small amount of tar precipitation;
[0041] 3) The dedusted biomass gas passes through the condenser 2 for most of the tar condensation treatment. At this time, the automatic temperature control system adjusts the flow of the cooling water to condense most of the tar in the gas, and the condensed liquid tar enters the tar In the storage chamber 6, when the tar content reaches a certain level, the diving valve d opens
Example Embodiment
[0045] Example 3
[0046] This example is basically the same as Example 2, except that the biomass fuel gas used is produced by a biomass fluidized bed gasifier.
PUM
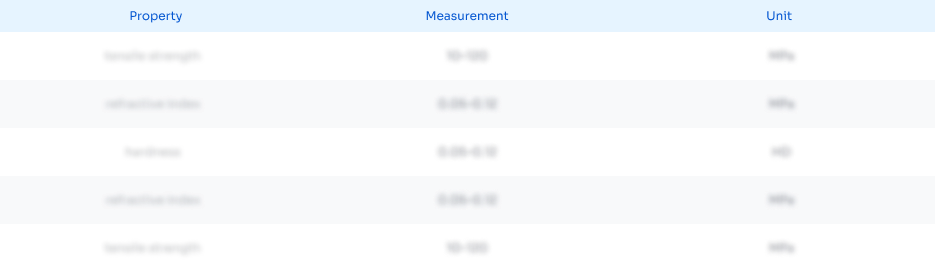
Abstract
Description
Claims
Application Information
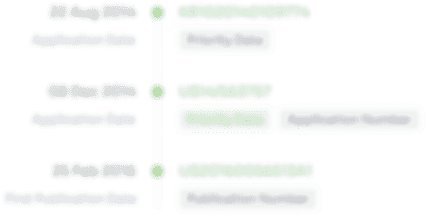
- R&D Engineer
- R&D Manager
- IP Professional
- Industry Leading Data Capabilities
- Powerful AI technology
- Patent DNA Extraction
Browse by: Latest US Patents, China's latest patents, Technical Efficacy Thesaurus, Application Domain, Technology Topic.
© 2024 PatSnap. All rights reserved.Legal|Privacy policy|Modern Slavery Act Transparency Statement|Sitemap