Control system and method for rotating speed of motor spindle of numerical control system
A technology of numerical control system and spindle speed, applied in the direction of electric speed/acceleration control, etc., can solve problems such as unreliable reliability, unstable control system, system blue screen crash, etc., and achieve non-interference stability, real-time control improvement, Good stability and reliability
- Summary
- Abstract
- Description
- Claims
- Application Information
AI Technical Summary
Benefits of technology
Problems solved by technology
Method used
Image
Examples
Embodiment Construction
[0031] The features of the control system and method of the present invention will be further described below in conjunction with the accompanying drawings.
[0032] Such as figure 1 As shown, the control system for the motor spindle speed of the numerical control system of the present invention includes an embedded Linux numerical control system master station 1 and a numerical control system slave station 2 . The master station 1 of the embedded Linux numerical control system includes a control module 11 and a master station interface module 12 . The numerical control system slave station 2 includes a servo device (or servo drive device) 22 with a slave station interface 21 and a motor 23 connected to the servo device 22 . In this embodiment, the master station interface module 12 is a standard network port RJ45 network port. The servo device 22 in the slave station 2 of the numerical control system is an AMK KW-r03 servo driver, and its control mode is speed control. The co
PUM
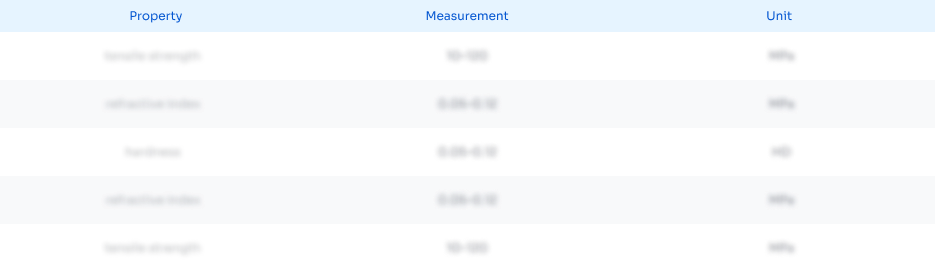
Abstract
Description
Claims
Application Information
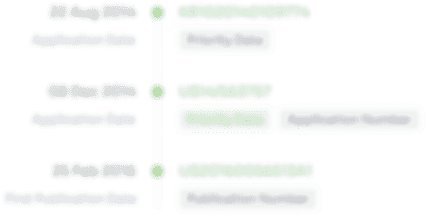
- R&D Engineer
- R&D Manager
- IP Professional
- Industry Leading Data Capabilities
- Powerful AI technology
- Patent DNA Extraction
Browse by: Latest US Patents, China's latest patents, Technical Efficacy Thesaurus, Application Domain, Technology Topic.
© 2024 PatSnap. All rights reserved.Legal|Privacy policy|Modern Slavery Act Transparency Statement|Sitemap