Process for machining water-cooling plate of high-power waveguide component
A processing technology and water-cooling plate technology, applied in metal processing equipment, manufacturing tools, auxiliary devices, etc., can solve the problems of reduced reliability, residual chips in the water tank, shortened service life of waveguide components, etc., and achieve the effect of improving accuracy
- Summary
- Abstract
- Description
- Claims
- Application Information
AI Technical Summary
Problems solved by technology
Method used
Image
Examples
Embodiment Construction
[0015] The present invention as Figure 1-4 As shown, the following steps are included: opening a meandering water tank 10 from the top surface of the water-cooling plate 1; opening threaded water inlets and outlets (including water port 101 and water port 2 102) from the side of the water-cooling plate 1, respectively communicating The water tank 10; the sealing plate 2 is added to the water tank 10 by vacuum brazing; before brazing, the ceramic threaded pipe 2 is respectively screwed into the threaded holes of the water inlet and outlet; after brazing, remove The ceramic threaded pipe 2.
[0016] The inner surface of the hole of the ceramic threaded pipe 2 is provided with an axial groove 32; so as to facilitate crushing;
[0017] The root of the ceramic threaded pipe 2 is provided with an outer hexagonal square opening 31 or an inner hexagonal square opening; so as to facilitate screwing in and out.
[0018] The water tank 10 is convex, with a small opening inside and a larg
PUM
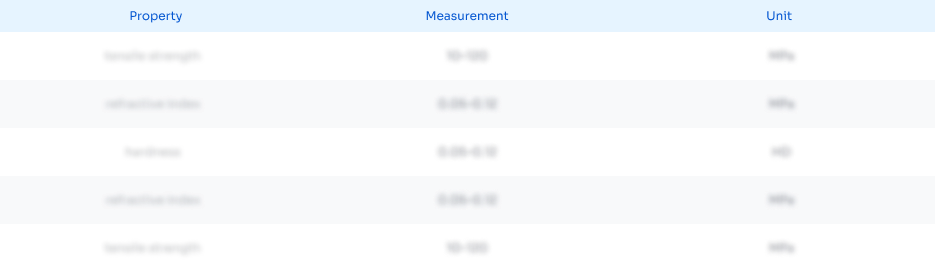
Abstract
Description
Claims
Application Information
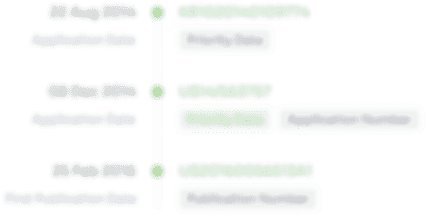
- R&D Engineer
- R&D Manager
- IP Professional
- Industry Leading Data Capabilities
- Powerful AI technology
- Patent DNA Extraction
Browse by: Latest US Patents, China's latest patents, Technical Efficacy Thesaurus, Application Domain, Technology Topic.
© 2024 PatSnap. All rights reserved.Legal|Privacy policy|Modern Slavery Act Transparency Statement|Sitemap