Blast furnace material-proportioning and material-loading method
A technology for blast furnaces and feeding carts, applied in the metallurgical field, can solve problems such as insufficient capacity of the intermediate weighing hopper, and achieve the effects of saving feeding time, saving investment costs, and saving investment and feeding time
- Summary
- Abstract
- Description
- Claims
- Application Information
AI Technical Summary
Problems solved by technology
Method used
Examples
Example Embodiment
[0011] A method for feeding blast furnace ingredients according to the present invention includes the following steps:
[0012] 1) The order of discharging the ore on the west side of the trough is: 4# sinter → 3# sinter → 1# lump ore → 2# sinter → 2# pellets → 1# sinter → 1# pellets → coke;
[0013] 2) The sequence of ore discharge at the east side of the trough is: 7# sinter → 8# sinter → 2# lump ore → 9# sinter → 2# flux → 10# sinter → 3# flux → 4# flux;
[0014] 3) After the above-mentioned ore discharge is completed, the slag plate valve of the middle hopper of East Ore is opened in place, and when discharging to the material truck is started, the 5# sintering weighing hopper starts to discharge; When the material truck is unloaded, the 6# sintering weighing hopper starts to discharge; the blast furnace batching and charging is completed.
[0015] In the present invention, when the 5# sintering and 6# sintering weighing hoppers are discharging materials to the conveyor belt, a part
PUM
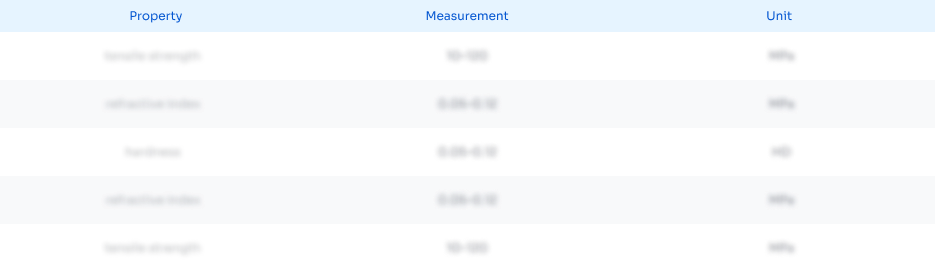
Abstract
Description
Claims
Application Information
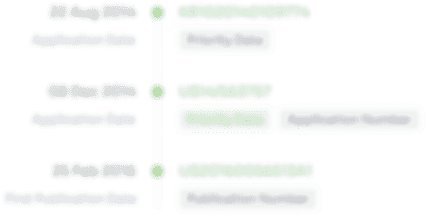
- R&D Engineer
- R&D Manager
- IP Professional
- Industry Leading Data Capabilities
- Powerful AI technology
- Patent DNA Extraction
Browse by: Latest US Patents, China's latest patents, Technical Efficacy Thesaurus, Application Domain, Technology Topic.
© 2024 PatSnap. All rights reserved.Legal|Privacy policy|Modern Slavery Act Transparency Statement|Sitemap