Modified catalyst for gaseous-state elemental mercury oxidation and preparation method of modified catalyst
A catalyst and elemental mercury technology, which is applied in the direction of physical/chemical process catalysts, chemical instruments and methods, separation methods, etc., can solve the problems of catalytic oxidation rate less than 15%, expensive, difficult to apply, etc., to achieve sustainable development, Long-lasting, low-cost effects
- Summary
- Abstract
- Description
- Claims
- Application Information
AI Technical Summary
Benefits of technology
Problems solved by technology
Method used
Image
Examples
Embodiment 1
[0028] Example 1 Anhydrous MnCl 2 Add in deionized water, stir evenly, and prepare different MnCl 2 Mass fraction of impregnation solution (MnCl 2 The solubility in water is shown in Table 1), and then the dried γ-Al 2 o 3 The pellets were respectively immersed in the above solution, stirred slightly and dipped for 6 h, dried at 80 °C for 8 h, heated at 200 °C for 2 h under nitrogen purging, and then heated at 380 °C for 3 h under nitrogen purging to prepare Catalyst MnCl with different content of catalytic components 2 / γ-Al 2 o 3 . Different MnCl 2 The mass fraction of each catalyst prepared by impregnating solution vs. Hg 0 The catalytic oxidation efficiency is shown in Table 2.
[0029] Table 1 MnCl 2 Solubility in water
[0030]
[0031] Table 2 Catalytic oxidation efficiency of catalyst
[0032]
Embodiment 2
[0033] Example 2 with anhydrous MnCl 2 As a catalytic component, (NH 4 ) 6 Mo 7 o 24 4H 2 O is used as a doping modification component, and (NH 4 ) 6 Mo 7 o 24 4H 2 O and MnCl 2 Mix according to different molar ratios, add deionized water and stir evenly to obtain MnCl-containing 2 The impregnation solution with a mass fraction of 15%, and then the dried γ-Al 2 o 3 The carrier pellets were respectively immersed in the above solution, stirred slightly and immersed for 6 h, then dried at 80 °C for 8 h, heated at 200 °C for 2 h under nitrogen purging, and then heated at 380 °C for 3 h under nitrogen purging. Catalyst MoO with different content of doped modification components and catalytic components prepared 3 -MnCl 2 / γ-Al 2 o 3 . (NH 4 ) 6 Mo 7 o 24 4H 2 O and MnCl 2 The effect of each catalyst on Hg prepared by impregnating solution mixed in different molar ratios 0 The catalytic oxidation efficiency is shown in Table 3.
[0034] Table 3 Catalytic oxid
Embodiment 3
[0036] Example 3 (NH 4 ) 6 Mo 7 o 24 4H 2 O and MnCl 2 Mix at 0.5% by mole ratio, add deionized water and stir evenly to obtain 2 and (NH 4 ) 6 Mo 7 o 24 The soaking liquid of mass fraction, all the other are identical with embodiment 2. Different MnCl 2 and (NH 4 ) 6 Mo 7 o 24 The mass fraction of each catalyst prepared by impregnating solution vs. Hg 0 The catalytic oxidation efficiency is shown in Table 4.
[0037] Table 4 Catalytic oxidation efficiency of modified catalysts
[0038]
PUM
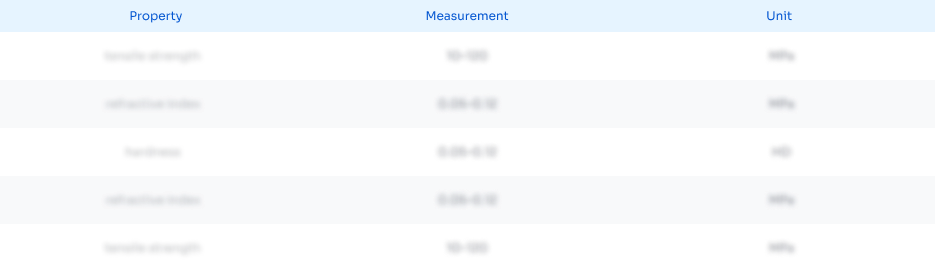
Abstract
Description
Claims
Application Information
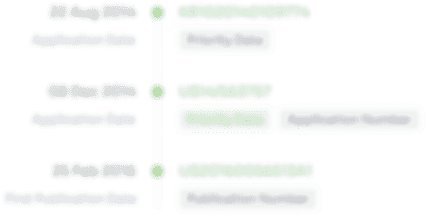
- R&D Engineer
- R&D Manager
- IP Professional
- Industry Leading Data Capabilities
- Powerful AI technology
- Patent DNA Extraction
Browse by: Latest US Patents, China's latest patents, Technical Efficacy Thesaurus, Application Domain, Technology Topic.
© 2024 PatSnap. All rights reserved.Legal|Privacy policy|Modern Slavery Act Transparency Statement|Sitemap