Novel high-chromium ferritic heat resistant steel and thermo-mechanical treatment process
A high-chromium ferrite, deformation heat treatment technology, applied in the field of high-chromium ferritic heat-resistant steel production, can solve the problems of high cost, complex production process, inability to guarantee corrosion resistance, etc., and achieves improved high temperature performance and thermal stability. Good performance and the effect of improving service temperature
- Summary
- Abstract
- Description
- Claims
- Application Information
AI Technical Summary
Benefits of technology
Problems solved by technology
Method used
Image
Examples
Embodiment 1
[0034] Example 1 The composition of high-chromium ferritic heat-resistant steel is shown in Table 1. The heat-resistant steel is processed into a cylindrical sample of Φ8×14mm, and the deformation heat treatment process experiment is carried out on the Gleeble1500D thermal simulation testing machine. The steps are: Heating at 5°C / s to 1100°C for 7 minutes to fully austenitize; then, cooling at -5°C / s to 850°C for 5s and then compressing and deforming, the deformation rate is 1 / s, and the deformation amount is 60% of time and space Cool to room temperature.
Embodiment 2
[0036] Example 2 The composition of high-chromium ferritic heat-resistant steel is shown in Table 1. The sample is processed into a cylinder of Φ8×14mm, and the deformation heat treatment process experiment is carried out on the Gleeble1500D thermal simulation testing machine. The steps are: s heat up to 1200°C for 5 minutes to fully austenitize, then cool to 800°C at 5°C / s and hold for 10s for 60% compression deformation at a deformation rate of 1 / s. After deformation, hold for 100s and then air cool to room temperature.
[0037] The sample after the above heat treatment was analyzed by OM morphology analysis and TEM morphology analysis. Figure 1(a) is the OM structure of Example 1, and Figure 1(b) is the OM structure of Example 2. It can be observed from Figure 1(a) that under this heat treatment process, the austenite grains cannot Dynamic recrystallization is carried out to obtain equiaxed grains without distortion, and the effect of deformation strengthening is improved;
PUM
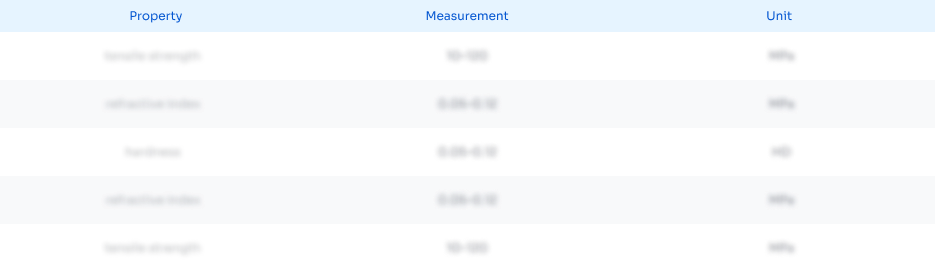
Abstract
Description
Claims
Application Information
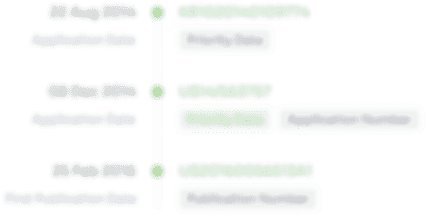
- R&D Engineer
- R&D Manager
- IP Professional
- Industry Leading Data Capabilities
- Powerful AI technology
- Patent DNA Extraction
Browse by: Latest US Patents, China's latest patents, Technical Efficacy Thesaurus, Application Domain, Technology Topic.
© 2024 PatSnap. All rights reserved.Legal|Privacy policy|Modern Slavery Act Transparency Statement|Sitemap