Stator and rotor punched sheet manufacture step by step craft
A technology of rotor punching and stator punching, which is applied in the field of generator stator and rotor punching, can solve the problems of high cost of progressive die, poor operation safety, and low work efficiency, so as to reduce labor intensity, improve safety and cost Reduced effect
- Summary
- Abstract
- Description
- Claims
- Application Information
AI Technical Summary
Benefits of technology
Problems solved by technology
Method used
Image
Examples
Embodiment Construction
[0026] The specific implementation, structure, features and effects provided by the present invention will be described in detail below in conjunction with the accompanying drawings and preferred embodiments.
[0027] Such as figure 1 The shown stamping process of stator and rotor of a motor adopts the automatic feeding of coil material 9, and it includes the following steps:
[0028] (1) Punch four guide holes 1, shaft holes 5, key slots 4, buckle slots 2 and all rotor slots 3, the obtained product structure diagram is as follows figure 2 shown.
[0029] (2) Punching out the rotor punching sheet: Positioning with four guide holes, punching the inner circle of the stator 10, the structure diagram of the obtained product is as follows image 3 As shown, the rotor punching sheet 6 is produced, and the structure schematic diagram of the obtained product is as follows Figure 4 shown.
[0030] (3) Stator groove punching: Position with four guide holes, punch out all the stator g
PUM
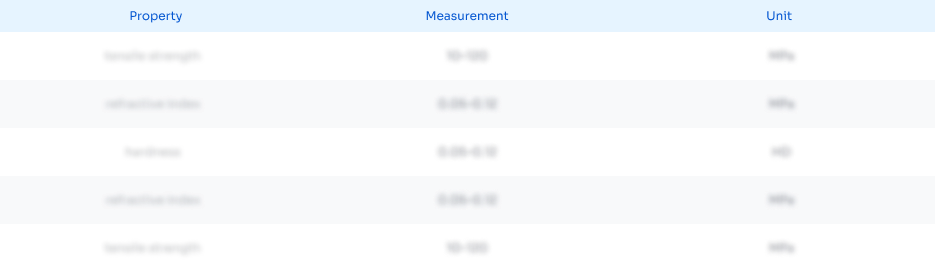
Abstract
Description
Claims
Application Information
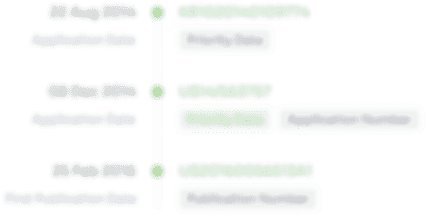
- R&D Engineer
- R&D Manager
- IP Professional
- Industry Leading Data Capabilities
- Powerful AI technology
- Patent DNA Extraction
Browse by: Latest US Patents, China's latest patents, Technical Efficacy Thesaurus, Application Domain, Technology Topic.
© 2024 PatSnap. All rights reserved.Legal|Privacy policy|Modern Slavery Act Transparency Statement|Sitemap