Tobacco leaf baking method
A baking method and tobacco leaf technology, applied in the field of flue-cured tobacco, can solve problems such as insufficient coal combustion, large coal consumption, and adverse environmental effects, and achieve the effects of avoiding adverse effects, reducing coal consumption, and reducing the cost of flue-cured tobacco
- Summary
- Abstract
- Description
- Claims
- Application Information
AI Technical Summary
Benefits of technology
Problems solved by technology
Method used
Image
Examples
Embodiment Construction
[0041] The embodiment of the present invention provides a method for curing tobacco leaves, which is used to improve the quality of tobacco leaf curing and at the same time make the coal burn more fully, greatly reduce the coal consumption, reduce the cost of flue-cured tobacco and avoid adverse effects on the environment.
[0042] In order to make the purpose, features and advantages of the present invention more obvious and understandable, the technical solutions in the embodiments of the present invention will be clearly and completely described below in conjunction with the accompanying drawings in the embodiments of the present invention. Obviously, the following The described embodiments are only some, not all, embodiments of the present invention. Based on the embodiments of the present invention, all other embodiments obtained by persons of ordinary skill in the art without making creative efforts belong to the protection scope of the present invention.
[0043] see figu
PUM
Property | Measurement | Unit |
---|---|---|
Thickness | aaaaa | aaaaa |
Abstract
Description
Claims
Application Information
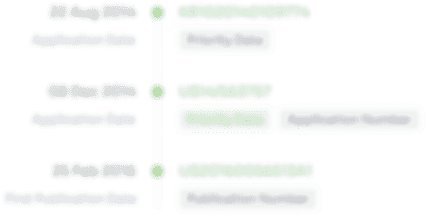
- R&D Engineer
- R&D Manager
- IP Professional
- Industry Leading Data Capabilities
- Powerful AI technology
- Patent DNA Extraction
Browse by: Latest US Patents, China's latest patents, Technical Efficacy Thesaurus, Application Domain, Technology Topic.
© 2024 PatSnap. All rights reserved.Legal|Privacy policy|Modern Slavery Act Transparency Statement|Sitemap