Preparation method of modified organic silicon resin/silicon carbide compounded abrasive
A composite abrasive and silicone technology, applied in the field of abrasives, can solve the problems of single component and poor effect, and achieve the effect of improving mechanical strength, reducing use cost and ideal cleaning effect
- Summary
- Abstract
- Description
- Claims
- Application Information
AI Technical Summary
Problems solved by technology
Method used
Examples
Example Embodiment
[0019] Example 1
[0020] The first step, the preparation of modified silicone resin: 0.5Kg of hydroxyethyl methacrylate, 0.3Kg of polyisocyanate, 1.0Kg of polyethylene terephthalate, 0.2Kg of methylphenyldimethoxysilane, 3.5Kg of polyphenylsiloxane and 0.4Kg of alkyl polydimethylsiloxane were put into the reactor, 5Kg of deionized water was added, stirred evenly, 0.05Kg of cumene hydroperoxide was added, and the temperature was 155°C. The reaction was carried out for 4 hours, and after the reaction finished, the modified silicone resin was obtained;
[0021] The second step, SiC coating: put the SiC powder with a particle size of 0.5mm into the chemical vapor deposition reaction chamber, use ethyl orthosilicate as the raw material, evacuate to 10Pa, and pass argon as the protective gas, argon The gas flow rate is 30sccm, the reaction chamber is preheated to 550°C, the raw material temperature is 115°C, and the coating starts. The rotation rate of the reaction chamber is 30r /
Example Embodiment
[0023] Example 2
[0024] The first step, the preparation of modified silicone resin: 1.6Kg of hydroxyethyl methacrylate, 0.7Kg of polyisocyanate, 2.5Kg of polyethylene terephthalate, 0.5Kg of methylphenyldimethoxysilane, 5.0Kg of polyphenylsiloxane and 0.7Kg of alkyl polydimethylsiloxane were put into the reactor, 10Kg of deionized water was added, stirred evenly, 0.25Kg of cumene hydroperoxide was added, and the temperature was 155°C. The reaction was carried out for 4 hours, and after the reaction finished, the modified silicone resin was obtained;
[0025] The second step, SiC coating: put 0.5mm SiC powder into the chemical vapor deposition reaction chamber, use ethyl orthosilicate as the raw material, evacuate to 10Pa, pass argon as the protective gas, and the gas flow rate is 30sccm, the reaction The chamber was preheated to 500°C, the raw material temperature was 115°C, and the coating was started. The rotation rate of the reaction chamber was 30 r / min, and the coatin
Example Embodiment
[0027] Example 3
[0028] The first step, the preparation of modified silicone resin: 1.1Kg of hydroxyethyl methacrylate, 0.5Kg of polyisocyanate, 1.6Kg of polyethylene terephthalate, 0.3Kg of methylphenyldimethoxysilane, 4.2Kg of polyphenylsiloxane and 0.5Kg of alkyl polydimethylsiloxane were put into the reactor, 7Kg of deionized water was added, stirred evenly, 0.15Kg of cumene hydroperoxide was added, and the temperature was 155°C. The reaction was carried out for 4 hours, and after the reaction finished, the modified silicone resin was obtained;
[0029] The second step, SiC coating: put 0.5mm SiC powder into the chemical vapor deposition reaction chamber, use ethyl orthosilicate as the raw material, evacuate to 10Pa, pass argon as the protective gas, and the gas flow rate is 30sccm, the reaction The chamber is preheated to 550°C, the raw material temperature is 115°C, and the coating is started. The rotation rate of the reaction chamber is 30 r / min, and the coating rea
PUM
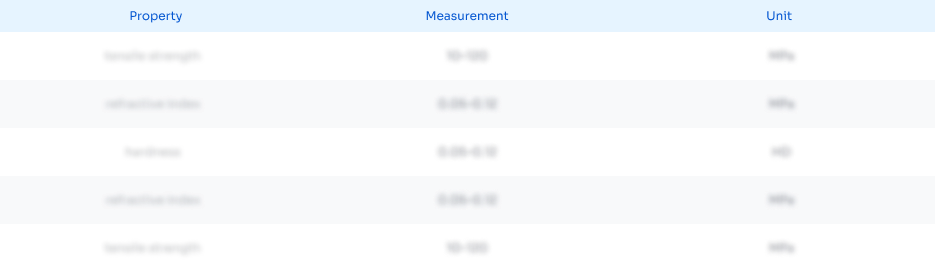
Abstract
Description
Claims
Application Information
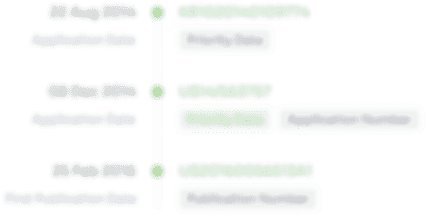
- R&D Engineer
- R&D Manager
- IP Professional
- Industry Leading Data Capabilities
- Powerful AI technology
- Patent DNA Extraction
Browse by: Latest US Patents, China's latest patents, Technical Efficacy Thesaurus, Application Domain, Technology Topic.
© 2024 PatSnap. All rights reserved.Legal|Privacy policy|Modern Slavery Act Transparency Statement|Sitemap