Lubricating oil filtering system for turbine body
A technology for steam turbines and lubricating oil, applied in mechanical equipment, engine components, machines/engines, etc., can solve the problems of temporary pipeline material and installation costs, low lubricating oil circulation rate, etc., to increase the circulation flushing rate and reduce the circulation flushing. The effect of time and oil filtering speed
- Summary
- Abstract
- Description
- Claims
- Application Information
AI Technical Summary
Benefits of technology
Problems solved by technology
Method used
Image
Examples
Embodiment Construction
[0010] The present invention will be further described below in conjunction with the accompanying drawings and embodiments.
[0011] The lubricating oil filter system of the steam turbine body includes the oil tank 1 and the oil inlet pipe 4 and the oil return pipe 5 connected between the oil tank 1 and the bearings of the steam turbine. The oil tank 1 is equipped with an auxiliary oil pump 2, and the oil tank 1 and the oil inlet pipes of each bearing 4 is provided with a flushing filter 3, the flushing filter 3 is provided with a filter element, and each bearing has a bearing bush 6, and each bearing bush 6 is provided with each bearing bush oil inlet pipe 7 and each bearing bush oil return pipe 8, and each bearing bush oil inlet The pipeline 7 and the oil return pipeline 8 of each bearing pad are short-circuited into the temporary pipeline 9 .
[0012] When the oil filtering system is running, the auxiliary oil pump 2 is started, and the turbine oil enters the system pipeline t
PUM
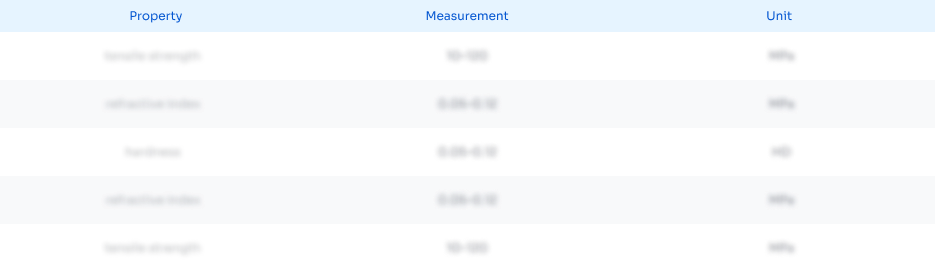
Abstract
Description
Claims
Application Information
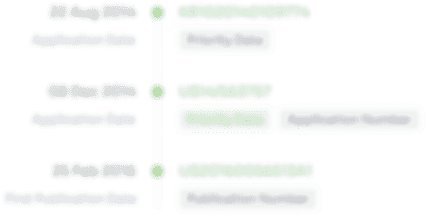
- R&D Engineer
- R&D Manager
- IP Professional
- Industry Leading Data Capabilities
- Powerful AI technology
- Patent DNA Extraction
Browse by: Latest US Patents, China's latest patents, Technical Efficacy Thesaurus, Application Domain, Technology Topic.
© 2024 PatSnap. All rights reserved.Legal|Privacy policy|Modern Slavery Act Transparency Statement|Sitemap