Ultra-thin PE (polyethylene) film for packaging bag
An ultra-thin, packaging bag technology, applied in the field of plastic film, can solve problems such as melt fracture, poor film transparency, affecting product molding and quality, and achieve good heat sealing performance and good anti-aging performance
- Summary
- Abstract
- Description
- Claims
- Application Information
AI Technical Summary
Benefits of technology
Problems solved by technology
Method used
Image
Examples
example 1
[0022] An ultra-thin PE film for packaging bags, comprising the following components according to the mass fraction ratio:
[0023]
[0024] The above-mentioned components according to the mass fraction ratio can be produced according to the process: raw material weighing, metering and stirring of various raw materials, feeding, melt extrusion, film shaping and cooling, traction, cutting and coiling, and the ultra-thin film can be produced. Type PE film, experiments show that the ultra-thin PE film can still maintain the same physical and chemical indicators when the thickness is only 80% of the current plastic film thickness, and has better transparency and no linear lines.
example 2
[0026] An ultra-thin PE film for packaging bags, comprising the following components according to the mass fraction ratio:
[0027]
[0028] The above-mentioned components according to the mass fraction ratio can be produced according to the process: raw material weighing, metering and stirring of various raw materials, feeding, melt extrusion, film shaping and cooling, traction, cutting and coiling, and the ultra-thin film can be produced. Type PE film. Experiments show that the ultra-thin PE film can also maintain the same physical and chemical indicators when the thickness is only 80% of the current plastic film thickness, and has better transparency and no linear lines.
example 3
[0030] An ultra-thin PE film for packaging bags, comprising the following components according to the mass fraction ratio:
[0031]
[0032] The above-mentioned components according to the mass fraction ratio can be produced according to the process: raw material weighing, metering and stirring of various raw materials, feeding, melt extrusion, film shaping and cooling, traction, cutting and coiling, and the ultra-thin film can be produced. Type PE film. Experiments show that the ultra-thin PE film can maintain the same physical and chemical indicators when the thickness is only 80% of the current plastic film thickness, and has better transparency, no linear lines, meets the drop test, and has a tensile strength higher than The national standard is 20%, and the shelf life of the film is 6-8 months longer than the current product.
PUM
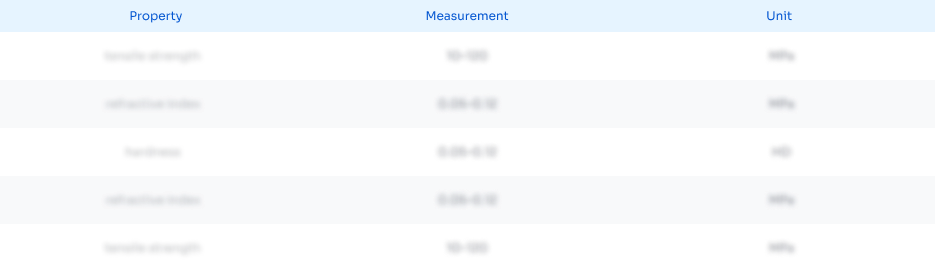
Abstract
Description
Claims
Application Information
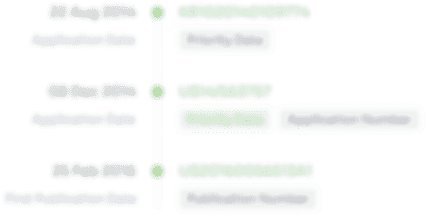
- R&D Engineer
- R&D Manager
- IP Professional
- Industry Leading Data Capabilities
- Powerful AI technology
- Patent DNA Extraction
Browse by: Latest US Patents, China's latest patents, Technical Efficacy Thesaurus, Application Domain, Technology Topic.
© 2024 PatSnap. All rights reserved.Legal|Privacy policy|Modern Slavery Act Transparency Statement|Sitemap