Turbine blade with step gap cooling structure on pressure surface
A technology of cooling structure and turbine guide vanes, applied in stators, engine components, machines/engines, etc., can solve the problems of decreased cooling effect of cold air, cooling and gas mixing, etc., to achieve simple and convenient maintenance process, reduction of aerodynamic losses, manufacturing The effect of reducing the difficulty of the process
- Summary
- Abstract
- Description
- Claims
- Application Information
AI Technical Summary
Problems solved by technology
Method used
Image
Examples
Embodiment Construction
[0012] The present invention will be further described in detail below in conjunction with the accompanying drawings.
[0013] refer to figure 1 , 2 As shown, the present invention is a novel film cooling structure suitable for a turbine guide vane of a gas turbine engine. The biggest feature of this new film cooling structure is that it adopts a stepped slot-out cooling structure to replace conventional film cooling holes. The stepped slot outflow structure is composed of the outer sheet (5) and the inner sheet (6) located in the blade base (1), and the outer sheet (5) and the inner sheet (6) form a shape on the surface of the blade. Stepped aerodynamic shape. The stepped slot structure can be arranged on the leading edge section (7) and the middle section (10) of the pressure surface of the turbine blade. In the outlet slot (2) of the cooling structure, 3 to 10 connecting ribs (3) can be arranged at the height of the blade between the outer sheet (5) and the inner sheet (6)
PUM
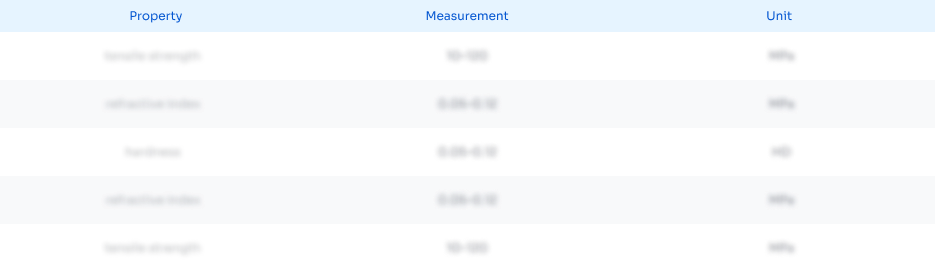
Abstract
Description
Claims
Application Information
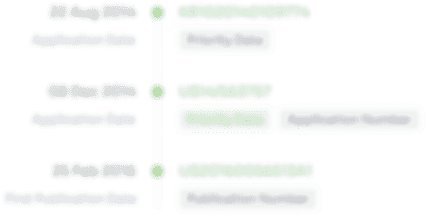
- R&D Engineer
- R&D Manager
- IP Professional
- Industry Leading Data Capabilities
- Powerful AI technology
- Patent DNA Extraction
Browse by: Latest US Patents, China's latest patents, Technical Efficacy Thesaurus, Application Domain, Technology Topic.
© 2024 PatSnap. All rights reserved.Legal|Privacy policy|Modern Slavery Act Transparency Statement|Sitemap