Consumable electrode gas shielded arc deposition three-dimensional printing method
A melting electrode gas, three-dimensional printing technology, applied in arc welding equipment, manufacturing tools, welding equipment and other directions, can solve the problem that the MIG principle can not meet the three-dimensional printing and other problems, achieve the improvement of metallographic structure and its uniformity, low cost, shape The effect of improved precision and surface quality
- Summary
- Abstract
- Description
- Claims
- Application Information
AI Technical Summary
Benefits of technology
Problems solved by technology
Method used
Image
Examples
Embodiment 1
[0020] The gas-shielded arc cladding three-dimensional printing method of the melting electrode comprises the following steps:
[0021] (1) Design a three-dimensional digital model of metal components in three-dimensional software, use three-dimensional printing system software to slice the three-dimensional digital model, generate multi-layer two-dimensional data slices, and the slice thickness is 1mm, and analyze to form a processing route;
[0022] (2) Using a welding torch to form a single-layer metal member by welding according to the processing route, the diameter of the fuse in the welding torch is 0.08mm, the welding voltage is 20V, the welding current is 2A, and the traveling speed is 12mm.s -1 , wire feeding speed 0.5mm.s -1 And the shielding gas pressure is 5Mpa; the torch includes a fuse 1 in the center of the nozzle, a shielding gas 2 arranged around the periphery of the fuse, and an electrode 4 connected to the fuse 1 and the three-dimensional printing platform 3 re
Embodiment 2
[0025] The gas-shielded arc cladding three-dimensional printing method of the melting electrode comprises the following steps:
[0026] (1) Design a three-dimensional digital model of metal components in three-dimensional software, use three-dimensional printing system software to slice the three-dimensional digital model, generate multi-layer two-dimensional data slices, and the slice thickness is 1mm, and analyze to form a processing route;
[0027] (2) Use a welding torch to form a single-layer metal member by welding according to the processing route. The diameter of the fuse in the welding torch is 1.5mm, the welding voltage is 14V, the welding current is 20A, and the traveling speed is 1mm.s -1 , wire feeding speed 15mm.s -1 And the shielding gas pressure is 2Mpa; the torch includes a fuse 1 in the center of the nozzle, a shielding gas 2 arranged around the periphery of the fuse, and an electrode 4 connected to the fuse 1 and the three-dimensional printing platform 3 respec
Embodiment 3
[0030] The gas-shielded arc cladding three-dimensional printing method of the melting electrode comprises the following steps:
[0031] (1) Design a three-dimensional digital model of metal components in three-dimensional software, use three-dimensional printing system software to slice the three-dimensional digital model, generate multi-layer two-dimensional data slices, and the slice thickness is 1mm, and analyze to form a processing route;
[0032] (2) Use a welding torch to form a single-layer metal member by welding according to the processing route. The diameter of the fuse in the welding torch is 1mm, the welding voltage is 18V, the welding current is 10A, and the traveling speed is 8mm.s -1 , wire feeding speed 10mm.s -1 And the shielding gas pressure is 3Mpa; the torch includes a fuse 1 in the center of the nozzle, a shielding gas 2 arranged around the periphery of the fuse, and an electrode 4 connected to the fuse 1 and the three-dimensional printing platform 3 respecti
PUM
Property | Measurement | Unit |
---|---|---|
Diameter | aaaaa | aaaaa |
Thickness | aaaaa | aaaaa |
Abstract
Description
Claims
Application Information
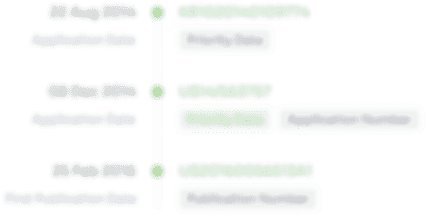
- R&D Engineer
- R&D Manager
- IP Professional
- Industry Leading Data Capabilities
- Powerful AI technology
- Patent DNA Extraction
Browse by: Latest US Patents, China's latest patents, Technical Efficacy Thesaurus, Application Domain, Technology Topic.
© 2024 PatSnap. All rights reserved.Legal|Privacy policy|Modern Slavery Act Transparency Statement|Sitemap