Method for prolonging service life of KR stirring head
A technology of stirring head and service life, which is applied in the field of improving the service life of KR stirring head, can solve the problems of short service life of KR stirring head, achieve the effect of shortening stirring time, increasing service life and reducing temperature stress
- Summary
- Abstract
- Description
- Claims
- Application Information
AI Technical Summary
Benefits of technology
Problems solved by technology
Method used
Image
Examples
Embodiment 1
[0029] The present embodiment is a 300t KR desulfurization station, the diameter of the molten iron ladle used is 4150mm, and the depth of the molten iron after 300t molten iron is loaded is 4500mm. The blade length of the KR stirring head is designed to be 1453mm, and the ratio of the blade length of the KR stirring head to the diameter of the ladle is controlled to be 0.35. The area of the blade facing the iron of the KR stirring head is 1.87 square meters. The ratio to the area of the longitudinal section of the ladle is 0.10. Before the stirring head enters the molten iron and starts to stir, control the KR stirring head to bake for 5 minutes above the ladle. When the KR stirring head is baking above the ladle, the distance between the KR stirring head and the liquid surface of the ladle is 0.2m. During the desulfurization process, the maximum rotation speed of the KR stirring head is controlled to be 100rpm, the ratio of the immersion depth of the KR stirring head to th
Embodiment 2
[0031] The present embodiment is a 300t KR desulfurization station, the diameter of the molten iron ladle used is 4150mm, and the depth of the molten iron after 300t molten iron is loaded is 4500mm. The blade length of the KR stirring head is designed to be 1657mm. The ratio of the blade length of the KR stirring head to the diameter of the ladle is controlled to be 0.4. The area of the KR stirring head blade facing the iron is 2.01 square meters. The ratio to the area of the longitudinal section of the ladle is 0.10. Before the stirring head enters the molten iron and starts to stir, control the KR stirring head to bake for 15 minutes above the ladle. When the KR stirring head is baked above the ladle, the distance between the KR stirring head and the liquid surface of the ladle is 1.2m. During the desulfurization process, the maximum rotation speed of the KR stirring head is controlled to be 80rpm, the ratio of the immersion depth of the KR stirring head to the depth of mo
Embodiment 3
[0033]The present embodiment is a 300t KR desulfurization station, the diameter of the molten iron ladle used is 4150mm, and the depth of the molten iron after 300t molten iron is loaded is 4500mm. The blade length of the KR stirring head is designed to be 1867mm, and the ratio of the blade length of the KR stirring head to the diameter of the ladle is controlled to be 0.45. The area of the blade facing the iron of the KR stirring head is 2.24 square meters. The ratio to the area of the longitudinal section of the ladle is 0.10. Before the stirring head enters the molten iron and starts stirring, control the KR stirring head to bake for 20 minutes above the ladle. When the KR stirring head is baked above the ladle, the distance between the KR stirring head and the liquid surface of the ladle is 2m. During the desulfurization process, the maximum rotation speed of the KR stirring head is controlled to be 70rpm, the ratio of the immersion depth of the KR stirring head to the d
PUM
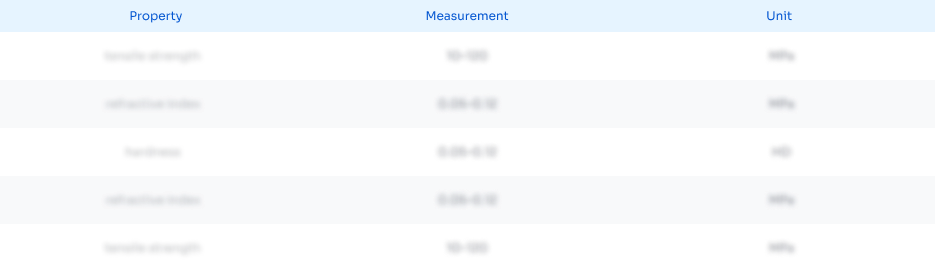
Abstract
Description
Claims
Application Information
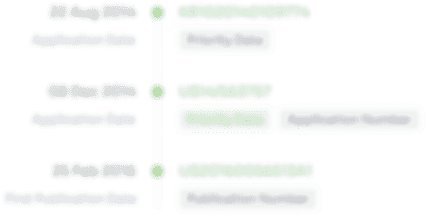
- R&D Engineer
- R&D Manager
- IP Professional
- Industry Leading Data Capabilities
- Powerful AI technology
- Patent DNA Extraction
Browse by: Latest US Patents, China's latest patents, Technical Efficacy Thesaurus, Application Domain, Technology Topic.
© 2024 PatSnap. All rights reserved.Legal|Privacy policy|Modern Slavery Act Transparency Statement|Sitemap