Marine oil-resistant and paint-aging-resistant instrument cable and manufacturing method thereof
A technology of instrument cable and manufacturing method, which is applied in the direction of cable/conductor manufacturing, insulating cable, insulating conductor/cable, etc. Fire-resistance performance, good protective effect
- Summary
- Abstract
- Description
- Claims
- Application Information
AI Technical Summary
Problems solved by technology
Method used
Image
Examples
Example Embodiment
[0018] Example one
[0019] Such as figure 1 As shown, the marine oil-resistant, paint-resistant and aging-resistant instrument cable of the present invention sequentially includes the following steps: uniformly extruding an insulating layer 2 on the outer periphery of the stranded copper conductor 1 to form an instrument cable insulated core, and twist the instrument cable insulated cores in pairs Combine to form a pair of twisted wires, fill the gaps of the twisted wires with a flame-retardant polypropylene fiber filler 3 to make the overall shape rounded, and then twist multiple pairs of twisted wires to form the instrument cable core, and then connect the instrument cable The outer periphery of the core is wrapped with a high thermal resistance coefficient flame-retardant and fire-resistant vertical tape 4, the outer periphery of the high thermal resistance coefficient flame-retardant and fire-resistant vertical tape 4 is covered with an armor braid 5, and the outer periphery of
Example Embodiment
[0023] Example two
[0024] Such as figure 1 As shown, the marine oil-resistant, paint-resistant and aging-resistant instrument cable of the present invention sequentially includes the following steps: uniformly extruding an insulating layer 2 on the outer periphery of the stranded copper conductor 1 to form an instrument cable insulated core, and twist the instrument cable insulated cores in pairs Combine to form a pair of twisted wires, fill the gaps of the twisted wires with a flame-retardant polypropylene fiber filler 3 to make the overall shape rounded, and then twist multiple pairs of twisted wires to form the instrument cable core, and then connect the instrument cable The outer periphery of the core is wrapped with a high thermal resistance coefficient flame-retardant and fire-resistant vertical tape 4, the outer periphery of the high thermal resistance coefficient flame-retardant and fire-resistant vertical tape 4 is covered with an armor braid 5, and the outer periphery of
Example Embodiment
[0028] Example three
[0029] Such as figure 1 As shown, the marine oil-resistant, paint-resistant and aging-resistant instrument cable of the present invention sequentially includes the following steps: uniformly extruding an insulating layer 2 on the outer periphery of the stranded copper conductor 1 to form an instrument cable insulated core, and twist the instrument cable insulated cores in pairs Combine to form a pair of twisted wires, fill the gaps of the twisted wires with a flame-retardant polypropylene fiber filler 3 to make the overall shape rounded, and then twist multiple pairs of twisted wires to form the instrument cable core, and then connect the instrument cable The outer periphery of the core is wrapped with a high thermal resistance coefficient flame-retardant and fire-resistant vertical tape 4, the outer periphery of the high thermal resistance coefficient flame-retardant and fire-resistant vertical tape 4 is covered with an armor braid 5, and the outer periphery
PUM
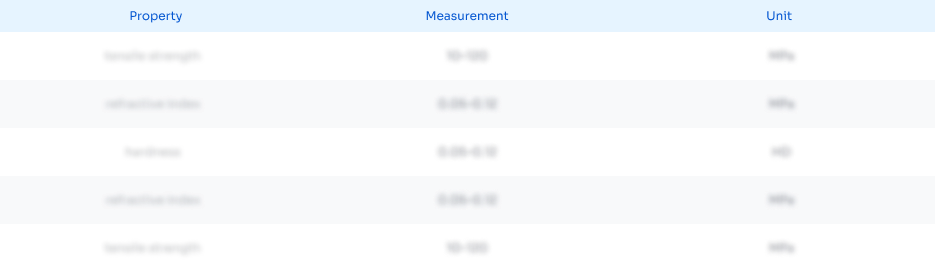
Abstract
Description
Claims
Application Information
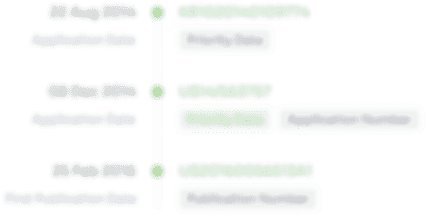
- R&D Engineer
- R&D Manager
- IP Professional
- Industry Leading Data Capabilities
- Powerful AI technology
- Patent DNA Extraction
Browse by: Latest US Patents, China's latest patents, Technical Efficacy Thesaurus, Application Domain, Technology Topic.
© 2024 PatSnap. All rights reserved.Legal|Privacy policy|Modern Slavery Act Transparency Statement|Sitemap