Preparation method of polyester FDY mother filament and monofilament thereof
A technology of mother silk and polyester, applied in the field of preparation of polyester FDY mother silk and its monofilament, can solve the problems that the production process cannot meet the market demand, the uneven dyeing performance of monofilament, etc. Effect
- Summary
- Abstract
- Description
- Claims
- Application Information
AI Technical Summary
Problems solved by technology
Method used
Examples
Example Embodiment
[0033] Example 1
[0034] A preparation method of polyester FDY mother yarn. The antibacterial polyester melt containing cuprous material is added to the conventional polyester melt pipeline by means of melt direct spinning pipeline addition, and the static mixer in the melt pipeline After mixing, melt spinning, cooling, drawing, heat setting and winding process to obtain polyester FDY split fiber mother yarn. The specific process is: spinning temperature of 292℃, wind temperature of 16~18℃, wind speed of 0.7~0.85m / s, drawing temperature of 95℃, drawing ratio of 1.8~2.2 times, heat setting temperature of 150℃, winding tension control It is 2.2~2.5cN, and the winding speed is 3900~4500m / min.
[0035] The mass ratio of antibacterial polyester melt containing cuprous material to conventional polyester melt is 1:8;
[0036] The number of holes in the mother yarn spinneret is 6~144 holes, and the denier of the mother yarn is 0.3~20D;
[0037] Monofilament production process: by dividing
Example Embodiment
[0056] Example 2
[0057] A preparation method of polyester FDY mother yarn. The antibacterial polyester melt containing cuprous material is added to the conventional polyester melt pipeline by means of melt direct spinning pipeline addition, and the static mixer in the melt pipeline After mixing, melt spinning, cooling, drawing, heat setting and winding process to obtain polyester FDY split fiber mother yarn. The specific process is: spinning temperature of 292℃, wind temperature of 16~18℃, wind speed of 0.7~0.85m / s, drawing temperature of 95℃, drawing ratio of 1.8~2.2 times, heat setting temperature of 150℃, winding tension control It is 2.2~2.5cN, and the winding speed is 3900~4500m / min.
[0058] The mass ratio of antibacterial polyester melt containing cuprous material to conventional polyester melt is 1:12;
[0059] The number of holes in the mother yarn spinneret is 6~144 holes, and the denier of the mother yarn is 0.3~20D;
[0060] Monofilament production process: by dividin
Example Embodiment
[0078] Example 3
[0079] A preparation method of polyester FDY mother yarn. The antibacterial polyester melt containing cuprous material is added to the conventional polyester melt pipeline by means of melt direct spinning pipeline addition, and the static mixer in the melt pipeline After mixing, melt spinning, cooling, drawing, heat setting and winding process to obtain polyester FDY split fiber mother yarn. The specific process is: spinning temperature of 292℃, wind temperature of 16~18℃, wind speed of 0.7~0.85m / s, drawing temperature of 95℃, drawing ratio of 1.8~2.2 times, heat setting temperature of 150℃, winding tension control It is 2.2~2.5cN, and the winding speed is 3900~4500m / min.
[0080] The mass ratio of the antibacterial polyester melt containing cuprous material to the conventional polyester melt is 1:15;
[0081] The number of holes in the mother yarn spinneret is 6~144 holes, and the denier of the mother yarn is 0.3~20D;
[0082] Monofilament production process: by
PUM
Property | Measurement | Unit |
---|---|---|
The average particle size | aaaaa | aaaaa |
Abstract
Description
Claims
Application Information
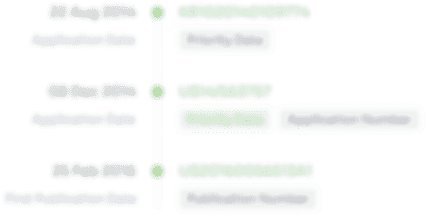
- R&D Engineer
- R&D Manager
- IP Professional
- Industry Leading Data Capabilities
- Powerful AI technology
- Patent DNA Extraction
Browse by: Latest US Patents, China's latest patents, Technical Efficacy Thesaurus, Application Domain, Technology Topic.
© 2024 PatSnap. All rights reserved.Legal|Privacy policy|Modern Slavery Act Transparency Statement|Sitemap